Discover how digital technologies and UK innovation can accelerate British manufacturing.
Want to find out more about different technologies and how they can support your business? View blogs, guides, useful downloads, and case studies from Made Smarter and our trusted partners.
You’ll be able to learn about specific business challenges and how to solve them, as well as discover real-life examples of new technologies in action.
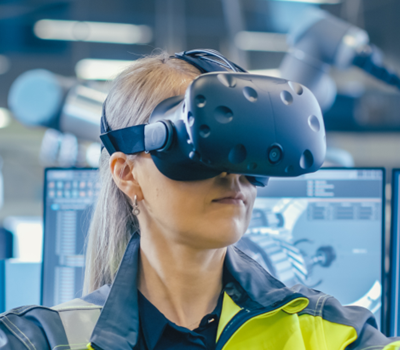
Catch up on the latest manufacturing insights with Made Smarter
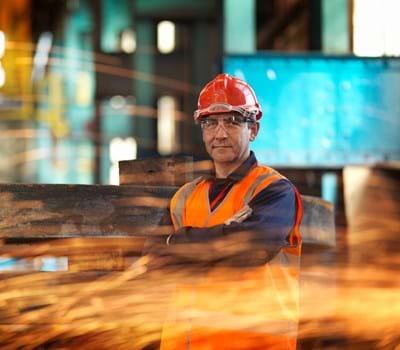
Discover how industrial digitalisation is transforming manufacturing.
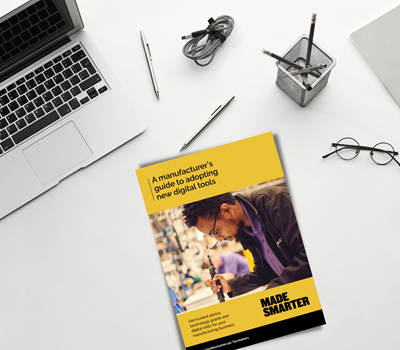
Articles, opinion pieces, and advice from those who have been there and done it.
Meet fellow manufacturers and hear about their journeys at our workshops, webinars, and conferences.
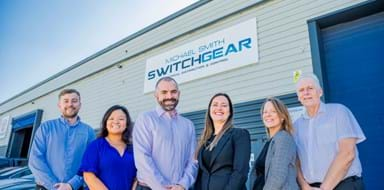
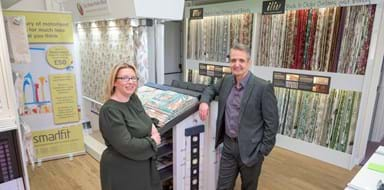
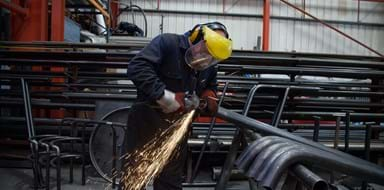
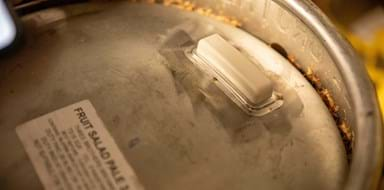
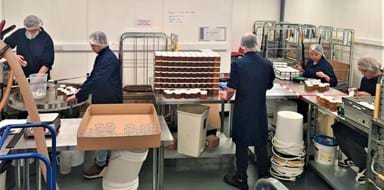
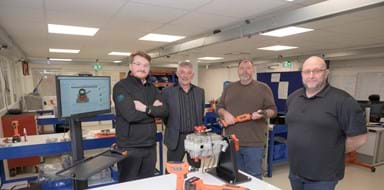
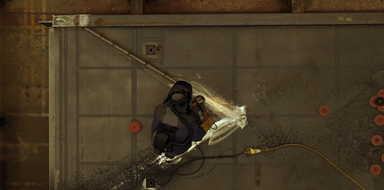
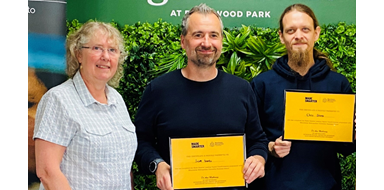
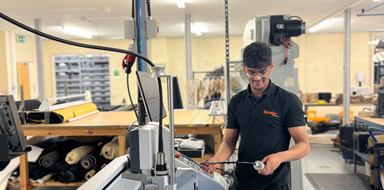
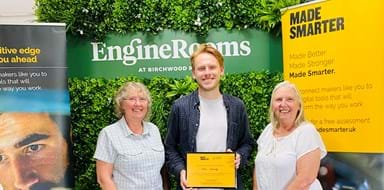
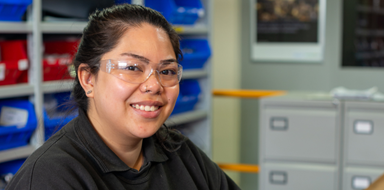
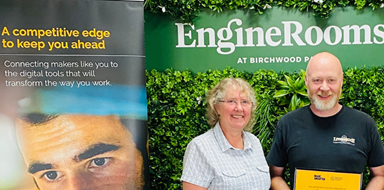