Made Smarter has been on an incredible journey over the last four years helping businesses navigate the pandemic and recover, negotiate supply chain disruption, and labour shortages, as well as focus on solutions to mitigate the energy crisis.
Despite a crosswind of challenges the programme has been an unparalleled success, offering impactful funded support to manufacturers across all sectors.
Paul McLaren, Chair of Made Smarter North West’s Steering Group, said: “Made Smarter has demonstrated that targeted support can be a catalyst for growth and a real enabler for change.
“UK manufacturing is moving into a phase where resilience is as important as it has ever been. Made Smarter is helping SMEs create robust plans to deliver impactful results.”
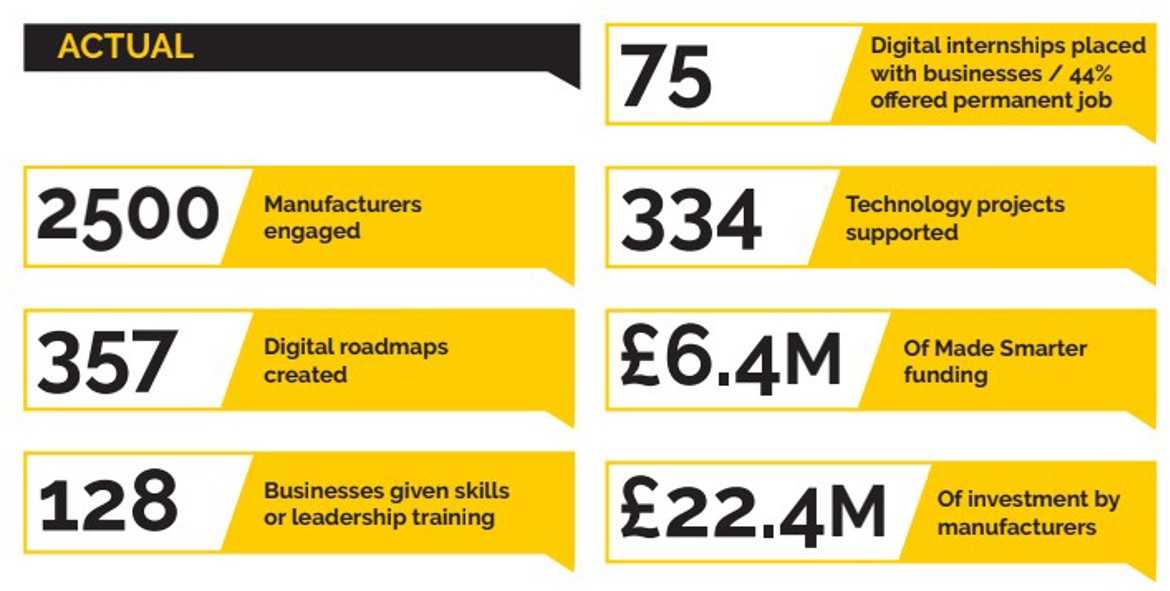
Actual
- 2,500 manufacturers engaged
- 357 digital roadmaps created
- 128 businesses given skills or leadership training
- 75 digital internships placed with businesses / 44% offered a permanent job
- 334 technology projects supported
- £6.4M of Made Smarter funding
- £22.4M of investment by manufacturers
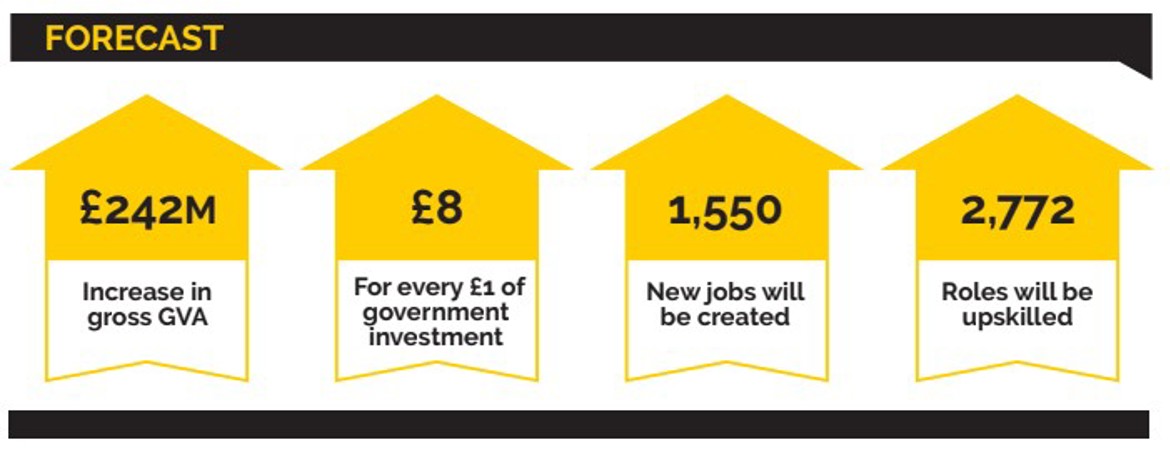
Forecast:
- £242M increase in gross GVA
- £8 for every £1 of government investment
- 1,550 new jobs will be created
- 2,772 roles will be upskilled
Digital transformation workshops (DTW)
Made Smarter advisers have taken 357 companies through the fully-funded digital transformation workshops to date. This process with a technology adviser and supported by the Organisational Development team, cuts through the jargon to identify the most effective technologies to overcome their operational challenges and any skills gaps.
These two short, focussed sessions: a two-hour diagnostic of the business’ products, services, processes and people; and a one-hour ‘findings’ presentation with recommendations and a digital adoption roadmap, a live document intended to help a business digitalise, one step at a time, in their own time.
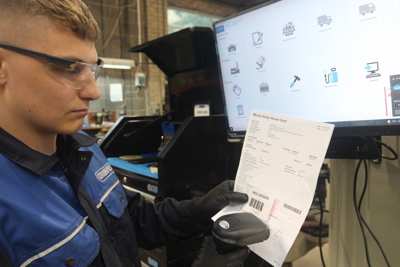
Case study - Joshua Greaves
The manufacturer of industrial mixing equipment used its experience of the digital transformation workshop to identify opportunities to invest in new technology.
Working with Made Smarter, Greaves found it was being hampered by a reliance on the use of manual recording and spreadsheets for logging of batches through each stage of production, stock control, purchasing and scheduling.
This meant it had no effective way of measuring rates of production, no visibility, and no way of implementing efficiency improvements.
The DTW process showed that a software solution could integrate business functions including sales, design, purchasing, planning, manufacturing and assembly.
The impact of real-time access to key data has been extensive. It has improved accuracy, scheduling and resource planning, cut lead times from four weeks to 48 hours, increased capacity and productivity, improved product costing accuracy, boosted sales, as well as reduced waste and carbon emissions.
Skills and leadership
Made Smarter’s OD team has supported 262 businesses with workforce, skills and leadership needs.
This includes creating 110 digitally-empowered leaders through its Leading Digital Transformation programme, a fast-track three-month course to create digitally-informed, empowered leaders, armed with a bespoke digitalisation strategy.
Meanwhile, the Leading Change for Digital Champions programme offers support for those leading change operationally on the shopfloor and is creating a network of digital champions who support each other with shared learning and experience.
Another area of success was the digital internships programme which paired 75 tech-savvy university students with businesses who benefitted from the up-to-date knowledge and expertise of the interns.
Almost half of interns secured permanent jobs at the end of their placements. Others benefitted from gaining work experience, which enabled participants to gain employment elsewhere.
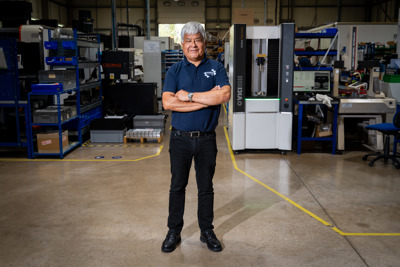
Case study - Beverston Engineering
The precision component manufacturer has been on a digital transformation journey with Made Smarter, creating a digital roadmap and investing in technology. But it has also benefited significantly from skills development.
Oliver Miller joined Beverston in 2020 through the internship programme. A postgraduate studying Aerospace Engineering at the time he was tasked with developing a new quality management system. He has since been recruited as the company’s Industry 4.0 Project Manager and has completed the Made Smarter Leading Digital Transformation programme.
Oliver Miller, Industry 4.0 Project Manager, said: “We have been on an incredible journey over the last few years, supported in part by Made Smarter, to create a smart factory and become an exemplar for other SMEs pursuing the same ambition.
“The digital internship initiative and Leading Digital Transformation programme are a great example of industry and academia working together to plug the skills gap and enabling businesses to take advantage of the opportunities Industry 4.0 offers”
Technology adoption
More than half (185) of the 334 technology projects supported by Made Smarter’s North West adoption programme focus on introducing technologies related to data collection and software systems.
As a result of integrating systems and consolidating data sources, business leaders have achieved real-time visualisation of their processes, been able to spot trends in production and labour, correct maintenance and quality issues, and minimise safety, business risk and operational downtime throughout their production.
Almost a quarter of the technology projects the programme has funded are for process control automation and robotics. Manufacturers are realising a raft of benefits including an increase in productivity, improved precision, consistency and quality, as well as opportunities to reduce operational costs by allowing machines to take on the burden of repetitive, low-value and sometimes dangerous work.
Around seven percent of projects have focussed on the Industrial Internet of Things (IIoT), using sensors to collect critical production data to gain valuable insights about the efficiency of operations. A similar number are adopting additive manufacturing to reduce waste and fast track prototyping, in order to create new products.
Meanwhile, early adopters who have already captured data and linked systems are using that activity as a platform for the next step, to focus on analytics and artificial intelligence to get more insight and value from their manufacturing operations.
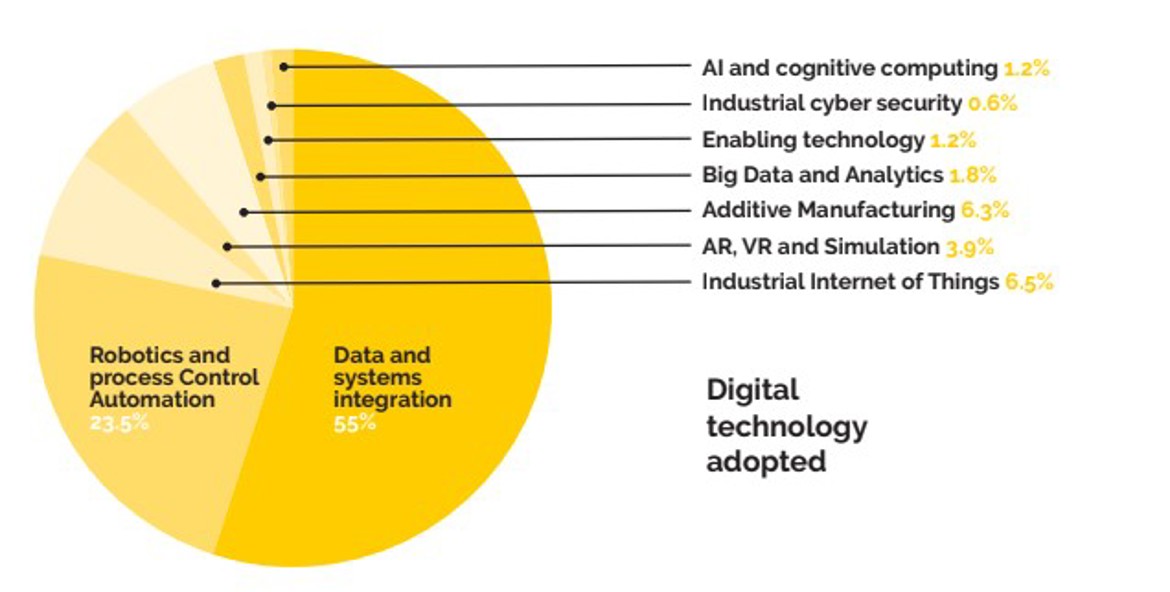
Sub-regional impact: Cumbria
Across Cumbria almost 200 manufacturers have engaged in the programme. Of these 50 businesses have engaged in technology projects which are forecast to create 125 jobs, upskill more than 200 roles and boost the Cumbrian economy by £24m.
The baked goods maker adopted two programmable ultrasonic cutting robots replacing a manual process. It is capable of slicing cake in an infinite number of sizes and shapes, and links to its ERP system to take into account customer orders, resources, and the fluctuation of the price of the ingredients.
The integrated solution increased productivity by 25%, improved accuracy and reduced wastage, and boosted profitability.
Read their story
A manufacturer of bike components invested in 3-axis CNC machining technology with a twin pallet setup or non-stop production. By bringing production in-house from subcontractors, the business has increased opportunities for customisation and innovation, and reduced costly delays and mistakes. The business is now doubling its manufacturing workforce and focusing on developing and marketing its own new bicycle drivetrain technology.
Read their story
Sub-regional impact: Cheshire & Warrington
Made Smarter has successfully engaged with 250 manufacturers in every corner of Cheshire and Warrington. Of these 30 businesses have engaged in technology projects which are forecast to create 85 jobs, upskill more than 200 roles and boost the sub-regional economy by £15m.
A plastic card manufacturer invested in digital printing technology which integrates with a bespoke software solution to read a card, check against a data file in real time, and then encode it.
The new ability to process up to 10,000 cards a day secured PCS a £1.5M identity card contract, increased turnover by 8% and created eight new jobs. It also opened up new opportunities for photo ID cards.
Read their story
The eco-friendly cleaning product manufacturer adopted new automated tube labelling and filling machinery for short production runs for its direct-to-consumer market. It has enabled the business to increase the rate of new product lines from 2 over an 18 month period to 22. This has driven a 25% growth increase and created two new jobs, while upskilling several existing roles.
Read their story
Sub-regional impact: Greater Manchester
More than 700 manufacturers in Greater Manchester have engaged in the programme with 92 adopting new technology. These investments are forecast to create 425 jobs, upskill almost 800 roles and add £64m to the economy.
The low protein food manufacturer replaced a manual process with an automated powder packaging machine, which includes an automated multi-head weigher and powder filler. This increases productivity 10-fold, reduces human error and waste, and is forecast to increase turnover by 30%. In addition, two operators are now focussed on more value-add activities such as sales and complex packing tasks.
Read their story
The puppet–maker adopted a world-first ability to 3D print stainless steel for the puppets used for the Oscar-winning stop-motion animation, Pinocchio. The innovation has paved the way for the use of 3D printed metal and cemented their position as leaders in their sector.
Read their story
Sub-regional impact: Lancashire
More than 500 manufacturers from Lancashire have engaged in the programme with 98 securing support for new technology projects. These are forecast to create almost 500 jobs, upskill more than 1,000 roles and boost the economy by £79m.
The manufacturer of vegan and free-from protein bars introduced bespoke automation solutions to enable high volume, high speed and accurate production, and integrate its systems, end to end from warehouse to despatch, enabling real-time visibility of its processes.
Nutree Life improved the accuracy and consistency of the product, quadrupled turnover and doubled its workforce.
Read their story
The manufacturer of specialist components for aerospace, power and automotive sectors adopted a bespoke machine condition monitoring solution which uses data collection and analysis to predict issues. This is helping ELE improve machine uptime and productivity by 10%, reduce maintenance spend by 10%, and improve accuracy and reliability by 10%. It also created an additional new role in the maintenance team and upskilled four existing staff.
Read their story
Sub-regional impact: Liverpool City Region
300 manufacturers from across the Liverpool City Region have engaged with Made Smarter. The programme has supported 60 technology projects which are forecast to create 385 jobs, upskill more than 375 roles and boost the economy by £52m.
The eco-friendly cleaning product maker invested in Industrial Internet of Things (IIoT) sensors to capture vital data about its blending, filling, labelling and packaging processes, before adopting a bespoke, cloud-based ERP solution to improve how it keeps track of orders, production and stock.
It enabled the business to meet increasing demand production capacity, and improve how it manages resources.
By introducing real-time monitoring and analytics Organica was able to make data-driven decisions and increase productivity by 20%, make processes 25% more efficient, reduce energy consumption by 10% per ton of product and reduce waste by up to 20%.
Read their story
The door and window manufacturer invested in a software solution to manage customer interactions and sales, and secondary software to integrate with production and dispatch.
As a result it increased back office productivity by 50% and freed up staff to focus on more high value tasks and sales opportunities. The business is now on track to double its turnover, contribute an extra £1M to the region’s GVA over the next three years and create 15 new jobs.
Read their story
Other Impacts: UK rollout
The North West programme has proved the value technology can bring to the manufacturing sector and become the blueprint of success, which now reaches other areas. Other programmes in the North East, Yorkshire and the Humber, the West Midlands, the East Midlands, and the West of England are also underway and starting to show positive results.
This has prompted the Government to commit to rolling out the adoption programme to all remaining English regions from 2025, and then potentially to Scotland, Wales and Northern Ireland from 2026, meaning all UK SME manufacturers will have access to the support they need to digitalise, decarbonise, and drive growth.
Other Impacts: Network
One of the legacy impacts of the programme has been the emergence of a network of SMEs to demonstrate how they have adopted technology.
“The biggest challenge for starting on the digital adoption journey is that people don’t know what they don’t know.
“Made Smarter has a blend of passionate skilled people who know what good looks like and demonstrates how achievable it is through case studies and its network of SMEs who have been through the programme. There’s nothing better than meeting other manufacturers who have your battle scars and share your pain and who can say, "I've been there and done that, and you can do it too’.” Mark Bayley-Smyth, Qualkem