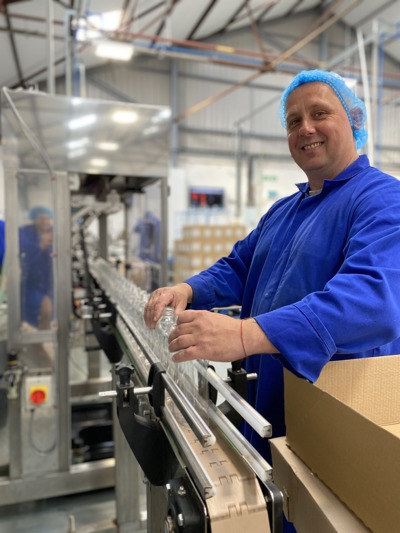
A cleaning product manufacturer has increased production capacity and transformed stock control, planning, and costing after investing in data-driven technology projects.
Organica UK Ltd makes environmentally friendly household cleaning products such as washing-up liquid, laundry detergents, fabric conditioner, and cleaning sprays for leading supermarket brands.
Since the Covid-19 pandemic, the Birkenhead business has experienced a growing demand for its products and needed to increase production capacity, and improve how it manages resources.
View the case studyWe have always been proactive and positive about the challenges and opportunities in digitalising, but Made Smarter support has enabled us to really hone our vision.
We have created a digital roadmap, brought in new skills, and fast-tracked our adoption of the right technologies we need to overcome our challenges and barriers to growth. We are now able to monitor and manage production on a scale that has so far not been possible.
Noel Doyle, Technical Director
A first project, supported by Made Smarter, used Industrial Internet of Things (IIoT) sensors to capture the volumes of ingredients going into and coming out of its blending tanks, the number of bottles being filled, capped and labelled on the filling lines, and the number of boxes on the packaging lines.
By introducing real-time monitoring and analytics Organica was able to make data-driven decisions and increase productivity by 20%.
The investment laid the foundations for a second project to adopt a bespoke, cloud-based ERP solution to improve how it keeps track of orders, production and stock.
Organica forecasts that it will make its production processes 25% more efficient, reducing energy consumption by 10% per ton of product and reducing waste by up to 20%.
With 200 product lines blended, packaged and distributed from its plant, and with an expanding customer base, Organica knew it was time to change the way it did things.
It was still using manual systems to manage its major operations, creating significant administration to keep track of orders, production and stock.
“Our planning systems were manual, outdated, inaccurate, time consuming and no longer able to cope with our current level of business,” Noel explained. It was a constant source of stress when disruptions in production arose.
“Controlling and minimising the downtimes in production due to material shortages had become an issue for some time.
“To facilitate further growth and maintain high quality for discerning customers, we needed to implement tighter control on our production and management processes.”
Understanding where the optimisation and control opportunities lie requires good quality live data and analysis. Digital transformation became essential.
Made Smarter’s digital transformation workshop helped Organica identify potential digital tools to solve its key business challenges and create a digital roadmap.
“Sitting down with an advisor to focus on our main issues was very valuable,” Noel said. “The key challenges were the need to enhance productivity on the filling lines by optimising the blending processes, as well as improve our packaging lines. We needed to automate data collection from the machinery, process and store it. We could then find ways of improving the efficiency, speed it up and increase productivity.
“Then we needed to connect our operations to enable forecasting and order placement, availability of raw materials, order processing, production scheduling, batch production, storage, distribution and cost management.”
Using further support from Made Smarter Organica’s invested in sensors to collect the data from its two blending tanks and three filling lines. A digital technology intern through Made Smarter was able to support the implementation.
These sensors now count bottles as they are filled, capped, labelled, and packed.
Data from these interconnected sensors is then displayed in real-time on a digital display.
Phase two is to pursue entire operational management using a bespoke, cloud-hosted ERP system which will integrate and automate its operations including its warehouse, stock control, distribution and finance.
This will display vital information to all the necessary managers on computer, tablets or their smartphone, and on a screen on the factory floor to show the status of orders.
The integration of sensors has enabled Organica to achieve better yields and machine uptime, reduce unnecessary maintenance stops and increase production output.
“We are able to do much more with what we have than ever before,” Noel said.
“With full visibility we can now more intelligently manage production and add to the bottom line, and achieve higher levels of customer satisfaction.
“Any stoppages and the cause is reported in real time so we can get it back up and running quickly.”
“We’ve seen a 20% increase in productivity already, and we know there’s more that can be achieved. Having the data is enabling us to make more informed decisions.”
Data analytics means that the management team can explore trends to find further efficiencies.
Organica forecasts that the new ERP system will increase stock management by at least 30% and product yield by 20%.
Oversight and control will increase efficiency, reduce rework of the product by 15%, reduce waste by 20%, and reduce energy consumption by 10% per ton of product.
“Having data from across our operations at our fingertips will make us much more lean and just-in-time,” Noel said. “By doing more with what we have we will reduce the number of deliveries and make our distribution more efficient to reduce our carbon footprint and become more sustainable.”
Following the project, Organica has been able to create eight new jobs, taking its headcount to 40 staff, and it anticipates creating more data analytics roles in the future.
It is forecast to increase turnover from £5m to £8m.
The workforce will be upskilled with operators retrained to understand the information provided by the ERP system; while managers will be trained to understand the impacts of the data analytics
Organica is now exploring where other digital tools can be applied to its operation, including using more sensors to integrate more elements of its manufacturing process such as the blending of products.
“Our digital transformation has been a fantastic experience so far,” Noel said. “The entire team has bought into the changes and we are all feeling really positive about the future.”