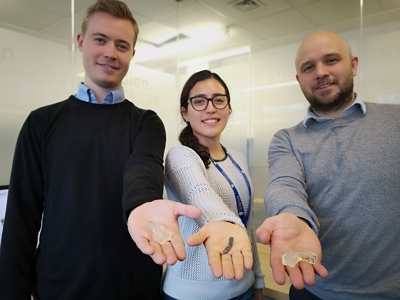
Formed as a spin-out from the University of Liverpool, the company – which is made up of engineers, scientists and orthopaedic veterinary surgeons – design and manufacture high performance implants from titanium using 3D printing.
Its Fusion TTA implant has already been used in over 4,000 operations to treat cruciate ligament injuries in companion animals. Earlier this year it launched the Fusion LEAP, an implant to specifically treat English Springer Spaniels which are predisposed to fractures in the lateral humeral condylar - the end of the bone at the top of the front leg.
Fusion Implants is keen to maintain its momentum as a pioneer in its sector.
View the Case StudyBy engaging with the Made Smarter program we are able to accelerate our research and development capacity for Fusion Implants, whilst also giving a graduate the opportunity to develop skills in additive manufacturing and implant design and development.
Dr Dan Jones, Managing Director of Fusion Implants
Its success with the Fusion LEAP product has inspired research and development of a similar anatomical implant to treat French Bulldogs, one of the most popular dog breeds in the UK, which are also prone to suffer humeral condylar fractures.
Dr Dan Jones, Managing Director of Fusion Implants, said the topography of French Bulldogs humeral condyle presents a challenge in plate contouring.
“At the moment a veterinary surgeon has to start with a straight plate and spending upwards of 20 minutes or so bending and contorting into an acceptable shape,” he said. “That means longer time in surgery for both the surgeon and for the animal, which can increase the risk of infection.
“As a fracture needs to be treated as a matter of urgency, it is not possible to customise a plate to the animal due to time constraints. However, it is possible to develop a set of stratified (based on a cohort of similar patients) generic plates which can be used in the surgical process.”
In order to develop a set of stratified generic plates, Fusion Implants is in the process of analysing hundreds of French Bulldog CT scans.
Using leading-edge biomedical software, it is plotting the measurements and identifying stratified samples. These groupings can be used to design anatomical bone plates.
Additive manufacturing will be used to build 3D plastic humerii models, and prototypes of the designed plates will be manufactured by laser powder bed fusion which can be tested.
Although at research and development stage, the aim by the end of the year is to have a working prototype which can be scaled-up commercially.
Dan said: “By engaging with the Made Smarter program we are able to accelerate our research and development capacity for Fusion Implants, whilst also giving a graduate the opportunity to develop skills in additive manufacturing and implant design and development.
“Our end goal is to have a prototype product which we can take to market, and a new employee.”
Fusion Implants believes the anatomical locking plate systems it has developed can be applied more widely to veterinary surgery. It is also exploring other common orthopaedic problems in companion animals which could benefit from this stratified approach to implant design.