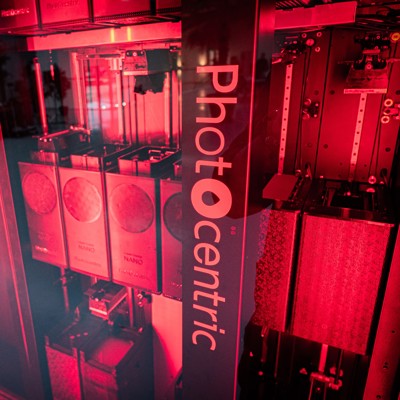
A 3D printing innovator has demonstrated the groundbreaking potential of a new faster, scalable and sustainable method of additive manufacturing.
Photocentric, based in Peterborough, led a consortium of injection moulding users including Games Workshop, Essentra Components and Unipart, as well software specialist Authentise and the Manufacturing Technology Centre (MTC), on a collaborative R&D project through Made Smarter Innovation’s Sustainable Smart Factory programme.
Innovation Case Study - PhotocentricThe LEAD (Low Energy Autonomous Digital) Factory designed and assembled a novel, fully automated production line powered by Photocentric’s 3D printing technology which takes liquid resin as an input and autonomously outputs functional plastic objects, at scales up to millions of parts.
The solution is capable of manufacturing one platform of parts every 20 seconds, up to around two tonnes of components per day.
The project has also introduced dynamic carbon footprint analysis and real-time reporting of material, energy consumption and consumables, demonstrating up to an 86% reduction in CO2e compared to injection moulding the same parts.
Chris Needham, Innovation Lead for Made Smarter Innovation, said: “Creating parts digitally has vast energy, productivity and waste reduction benefits.
“This was an incredible project which created a disruptive solution for digitally manufactured, 3D-printed parts that can be created entirely autonomously, more sustainably, and challenges the existing injection moulding techniques from overseas.
“This project shows how a single technology breakthrough can support manufacturing sectors as diverse as automotive components and leisure products – and can serve as an inspiration to others regarding how digitally driven solutions could benefit their sector.”
The Inspiration
While 3D printing has huge potential for manufacturing including more flexible production, mass customisation, reduced waste and emissions, it is predominantly used for prototyping or very low volume production.
Automating 3D printing is challenging at scale and, as such, no reliable ‘industrial scale’ solutions had previously existed.
Over the last 10 years, Photocentric has been innovating with its photopolymer 3D printing, developing a patented LCD-based process which uses display screens as a mask to encode full print layers at once.
A breakthrough came during the pandemic when the company built a manually-operated print farm to produce 4m face shields, demonstrating superior flexibility, speed and sustainability.
Through the LEAD project, Photocentric was able to pursue the development of a new method of digitally manufacturing parts in scale, autonomously, and test it by manufacturing a variety of different products: figurines, standoffs, electronic connectors, auto parts, and dental aligners.
The Innovation
The outcome of the project was JENI, a fully autonomous robotic 3D Printing manufacturing line.
JENI consists of custom robotics which rapidly move platforms of parts through the entire process – including printing, washing, and curing them, with no human intervention.
The system can be expanded, adding or removing nodes and modules, and is fully customisable to meet end-user requirements.
By inputting CAD directly, it allows any number of design variations for a single component without the need for separate injection moulding. CAD effectively becomes the tooling.
The solution is also capable of integrating with Manufacturing Execution System (MES) & Enterprise Resource Planning (ERP) systems to track the platforms, materials and parts, with Authentise providing nesting and slicing and inputting jobs to the system.
Meanwhile, the MTC produced a toolkit to track and analyse the carbon and the energy use of the whole process.
The Impact
JENI has unlocked the potential for the mass production of 3D printed parts, demonstrating a cheaper, faster and more sustainable approach.
CAD integration enables users to iterate, update and customise production-ready parts faster than injection moulding, while removing the need for re-tooling and eliminating downtime.
JENI records the precise amount of energy and material that has been used to manufacture a product and records the CO2e created for that part.
Validated testing by the MTC on a small plastic PCB clip produced by Essentra, one of the UK’s largest injection moulders, demonstrated an 86% reduction in CO2e.
If Essentra manufactured 100 million similar components annually with JENI, it could reduce CO2e by 727,200kg.
The solution makes 3D printing more affordable and agile. It opens up on-shoring and agile supply-chain opportunities by enabling local print-on-demand production, eliminating the environmental and economic burden of overseas manufacture, and the need for spare part stock storage.
Photocentric’s in-house chemistry team also developed new functional materials using plant-based and material waste streams, as well as two potential recycling routes for thermoset 3D printed resins.
The project has also led to new areas of innovation. Photocentric has developed a follow-on project to incorporate AI and machine learning into the JENI system to further enhance efficiency and throughput through optimised robotics and automation, rapid scheduling and related controls.
Paul Holt, CEO of Photocentric, said: “This project has been a thrilling demonstration of collaboration to achieve innovation. We have made a giant leap in terms of automating a previously manual process, enabling scale which didn’t exist, and driving forward the green agenda with a more sustainable approach to mass production.
“JENI was named after the spinning jenny, the ground-breaking invention which heralded the first industrial revolution. We believe this project can act as a trigger for starting the next digital industrial revolution of manufacturing, again here in the UK.”