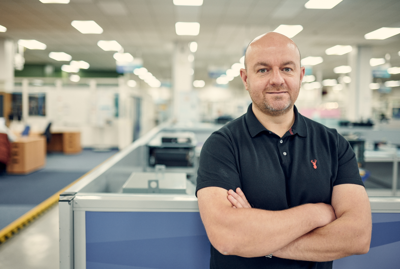
Atec Engineering Solutions, based in Salford, designs, manufactures, and repairs complex electronic and electro-mechanical equipment used in the aerospace, defense, nuclear, and oil and gas sectors.
But disparate IT and data processing systems, as well as being a long-standing business with sometimes outdated processes, were hampering growth and improvement.
Atec sought help from Made Smarter and created a digital transformation strategy, mapping out a roadmap of key challenges and solutions.
It was then successful in securing funding from the Industrial Strategy Challenge Fund’s (ISCF) Manufacturing Made Smarter (MMS) competition for a project to integrate its systems across the shop floor.
ATEC Solutions Case StudyPart of our problems before the project was that highly skilled, long-serving staff had their own black box of how to do things. Now our system is simplified and geared up to enable apprentices and new starters to understand the processes.
John Bowden, Managing Director
In 2019, Atec came to Made Smarter with a conundrum. It had an MRP/ERP system to help manage product workflow and labour requirements for a job, but it was striving to streamline processes and improve performance.
Reports were showing that it was taking too long to complete its core business, making and repairing its own product range, meaning capacity to manufacture third party products, a huge growth area, was being stifled.
Analysis through Made Smarter’s digital transformation workshop uncovered that different departments were not closing off jobs consistently or using the ERP system effectively, meaning department heads were creating workarounds to rectify issues with performance reports.
The workshop process brought key decision-makers around the same table to look at the problem with fresh eyes.
It determined that data integrity through a data cleanse and correcting errors, as well as centralising data stored disparately, would be a major step towards solving its problems and creating a pathway to new growth.
The business also had to focus on changing the culture and attitudes to move away from traditional ways of operating.
The results of correcting the data were immediate, with performance improving significantly.
With data it could rely on, Atec was able to focus on investing in technology as a next step along the roadmap.
The MMS project introduced a paperless shop floor, enabling its operators to work from tablets which integrate with an app and dashboards to visualise live data within its ERP/MRP system.
John Bowden, Managing Director, said: “The smart connected shop floor project was much more advanced than we initially considered but we knew that solving our challenges wasn’t enough, we needed to embark on digital transformation. And this was our chance.”
The investment integrated digital records relating to products which could be viewed, edited and managed via an app on a tablet. It replaced the physical packs of data sheets, drawings, specifications and instructions associated with every job, giving engineers everything they need at their fingertips.
Operators can also feed back any issues with parts and process into a ‘reliability database’ to identify any trends live, so they can be addressed quickly. And with live data, managers can monitor where a job is up to.
The system now allows the digital integration of customers’ bill of materials, which has removed the time-consuming manual processes of inputting data and reduced lead times from 7-10 days to half an hour.
The cumulative impact of its investment is that Atec is forecasting up to 10% increase in productivity.
The transformation has been received well by Atec’s customers such as BAE Systems, Rolls-Royce and Boeing.
John said: “The feedback has been amazing from partners. I have no doubt that the contracts we are winning have been partly due to our modernisation and the digital infrastructure we have invested in. They see this clean and modern factory, run by a forward-thinking, responsive and agile business.”
Having experienced the success of investing in technology, Atec has the confidence to take further steps.
Among them is exploring solutions to integrate data from the supply chain to its own systems to grow its build-to-print business.
John said: “We're a really forward-looking organisation. We love continuous improvement, and we knew we needed to get on the digitalisation journey. But we were stifled because we couldn’t see a case for introducing advanced technologies such as robotics and VR.
“But then Made Smarter arrived and the message was that experimenting with technology was good, but the real focus should be on solving your biggest challenge in the business.
“The expert analysis was enlightening and unlocked the honesty we needed to have those difficult conversations to overcome some entrenched ideas.
“While technology has transported us to where we are, the digital transformation workshop process has established a culture of challenging why and how we do things to unlock success.
“It is incredible to think that three years ago we started creating a digital roadmap with the ambition of a smart factory, and thanks to Made Smarter it has been accelerated by 10 or more years.
The cultural change has also repositioned Atec as a digital business which sits well with emerging talent.
John said: “Part of our problems before the project was that highly skilled, long-serving staff had their own black box of how to do things. Now our system is simplified and geared up to enable apprentices and new starters to understand the processes.
“The feedback from our recent recruits is that our digital journey makes us more appetising to the younger generation, which is exactly how we need to position our business and engineering as a whole.”