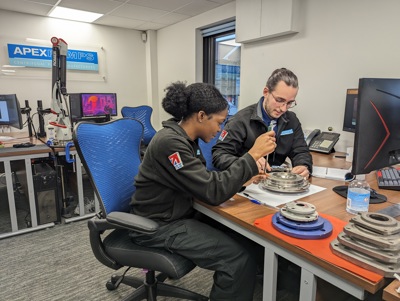
Apex Pumps is a Bristol-based manufacturer specialising in high-quality centrifugal pumps for industries including petrochemicals, aquaculture, and building services.
Since its founding in 1988, the company has focused on delivering durable and efficient products, ensuring every pump is designed and manufactured in the UK. As the business continued to grow, Apex Pumps recognised the need to refine its operations further, particularly in improving efficiency and enhancing its customer service processes.
The company had already taken steps towards digitalisation by implementing an Enterprise Resource Planning (ERP) system. However, as demand increased, Apex Pumps identified areas where technology could streamline operations even further. The process of generating technical quotations was time-consuming, often requiring significant manual input, which affected response times for customers. The company wanted to optimise this process, ensuring that quotations were delivered quickly and with greater accuracy. At the same time, Apex Pumps was keen to assess its overall efficiency and explore new digital tools that could help them stay competitive in an evolving industry.
Seeking expert guidance, Apex Pumps registered for the Made Smarter programme to gain a deeper understanding of how digital technology could enhance its operations. Specialists from Made Smarter and the National Composites Centre undertook a full assessment of its processes. Through this review, areas of inefficiency were identified, and a structured grading system was introduced to help prioritise improvements.
One of the key areas for development was the technical quotation process. By accessing grant funding through Made Smarter, Apex Pumps was able to invest in advanced pump selection software, which streamlined the quotation process significantly. This system allowed the company to generate accurate quotes much faster, ensuring that customers received precise recommendations in a shorter timeframe. Plans are now in place for a second phase of this development, which will introduce a self-service function, enabling customers to select pumps more efficiently without requiring manual input from the team.
As part of its digital transformation journey, Apex Pumps also made use of the Made Smarter internship programme, bringing in a fully funded intern with expertise in digital systems. The addition of this resource provided valuable support in implementing new technologies and helped drive forward the company’s digital initiatives.
The introduction of digital tools has had a significant impact on the efficiency and productivity of Apex Pumps. The new quotation system has greatly reduced the time required to generate technical quotes, allowing the business to respond to customer enquiries more quickly and with greater accuracy. This improvement has led to an enhanced customer experience, with clients benefiting from faster service and more precise product recommendations.
Beyond improving response times, the digital upgrades have also freed up valuable time for staff, allowing them to focus on higher-priority tasks rather than manual administrative work. The structured approach provided by Made Smarter has helped Apex Pumps pinpoint inefficiencies and prioritise the most effective solutions, ensuring that every investment in digital technology delivers tangible benefits. Additionally, the support provided through the internship programme has brought in fresh expertise, equipping the company with the skills needed to continue its digital transformation.
With the foundations of digitalisation now in place, Apex Pumps is committed to building on this progress. The company plans to continue integrating new digital tools into its operations, with a focus on further automating processes and enhancing efficiency. Investment in staff training will ensure that employees are equipped to make the most of new technologies, and future developments in digital systems will enable the company to maintain its competitive edge.
By working with Made Smarter, Apex Pumps has successfully modernised key aspects of its business, demonstrating how digital transformation can lead to meaningful improvements in efficiency, customer service, and long-term growth. With a clear strategy in place, the company is well-positioned to continue innovating and driving success in the manufacturing sector.