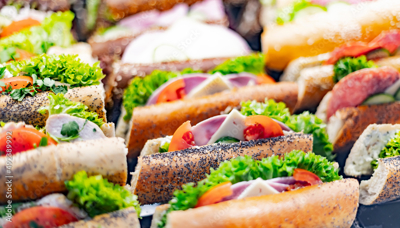
A prototype software platform offers food manufacturers the opportunity to share valuable data – increasing productivity, improving cashflow, boosting food quality, and reducing waste within the supply chain, with all the data locked into a secure blockchain.
It’s not something most of us think about when we buy a BLT or egg mayo baguette for lunch on the go, but a pre-packed sandwich has been through a lengthy and complex supply chain before you can bite into it.
Innovation Case Study - The Digital SandwichFrom primary producer to retailer, ingredients must be kept at correct temperatures at all times, and deliveries timed to the minute.
The fast-moving nature of the chain means mismatched supply and demand can lead to enormous waste – both food and financial. On top of that, as highlighted by a recent high-profile case of a sandwich causing a fatal allergic reaction, health and safety is paramount.
The Digital Sandwich project aims to bring increased traceability, security and accountability to the food supply chain by utilising the latest industrial digital technologies. “Currently, very little data is shared up and down the supply chain. It not only means different components may not be working in tandem with each other, but also that important information – such as food safety and regulatory data – can be difficult to access quickly,” explains Tom Hollands, Innovation and Technical Director at Raynor Foods, a leading UK pre-packed sandwich business, which is leading the project.
“The combination of technologies in Digital Sandwich enables detailed data to be shared across the complex supply chain, which lead to increased productivity, improves cash flow, help boost food quality and reduces the £15bn of food waste each year within in the supply chain.”
With £4m funding from the Made Smarter Innovation Challenge, Raynor Foods brought together a large consortium of food manufacturers, supply chain partners, suppliers, technology developers, and universities.
Using Raynor Foods’ sandwich supply chain as a use case, the project created a ‘sandwich’ of digital technologies – including Internet of Things (IoT), blockchain and artificial intelligence (AI) – into one unique platform.
“The world-first combination of technologies provides information at a granular level with the whole history of a product from primary production to point of sale,” explains Oliver Kinsey, Innovation Delivery Manager at IMS Evolve, lead IoT developer and project partner.
“Every item of food will have a digital identity that’s securely locked into the blockchain. For example, a manufacturer could scan a ham and the platform has data that tracks it to an individual pig identification tag on a farm and shows where it was slaughtered. Information that we collect from sensors on fridges show the product has been kept at safe temperatures and trackers on delivery trucks indicate when it will arrive at the factory.” As well as clear benefits in terms of ingredient traceability, the platform also helps maximise efficiency and reduce waste.
“Sandwich production is particularly vulnerable to the Bullwhip Effect, where a small change at one end of the supply chain can lead to increasing changes as it moves through. An increase in orders for BLTs from one retailer, for example, causes a sandwich manufacturer to increase its production by a bit more to compensate, which then causes the bacon, lettuce and tomato suppliers to increase even more – and much of this food is wasted,” explains Hollands.
“Digital Sandwich reduces this effect by enabling instant, real-time data to flow through the whole supply chain.”
Importantly, the platform allows small and medium-sized enterprises, who don’t usually have access to this kind of technology, to benefit – enabling every point of a supply chain to be optimised, from the smallest producer to the largest multinational.
Following on from the demonstrator platform, the project team plans to implement the technology through Raynor’s factory and supply chain as the next stage proof of concept.
The Digital Sandwich has potential applications beyond food manufacturing, too. “It could benefit any sector with complex, fast-moving supply chains that demand a high level of trust, such as pharmaceuticals, aerospace and automotive,” adds Hollands. “If this technology was widely adopted by UK Plc it would have a profound and positive impact on the economy.”