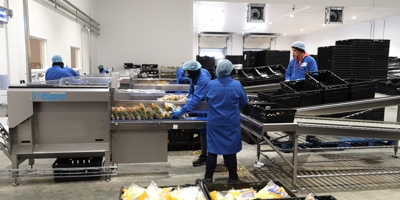
A Lancashire prepared salad manufacturer has embarked on an IT data and systems integration project which will help its factory process more, using less energy and creating less waste.
Len Wright Salads (LWS) started life as a one-man growing enterprise the 1960s and has flourished into a £46M turnover business covering 2,500 acres at Tarleton Moss - in the heart of England’s Salad Garden.
The 110 staff at its new £13M prepared salad factory process 8.9M kilos of baby leaf salad and 31m whole head lettuces each year, as well as vast quantities of celery, spinach, tomatoes and peppers, for supermarkets and restaurants across the UK, Ireland and France.
But LWS want to make its manufacturing process more energy efficient, reduce waste and increase sales.
It has put data and systems integration at the heart of the solution.
Using match funding from Made Smarter, LWS has been able to kick start an ambitious digital transformation journey, which will also support its supply chain - something it says would not be possible without Made Smarter.
Case Study - Len Wright SaladsMade Smarter has given us the confidence to drive forward this and the future phases of the transformation strategy which won’t just help Len Wright Salads, but secure the long-term economic and environmental sustainability of the salad growing industry in West Lancashire. Without Made Smarter investment the business will not be able to afford to undertake this and future phases of the transformation strategy.
Colin Charlesworth, Finance Director at Len Wright Salads
While the new prepared salad factory is using state-of-the-art bespoke machines to cut, clean, mix and bag salad, the systems work in silos and key data isn’t captured or shared.
Meanwhile, other parts of the organisation use software of a variety of ages, some of it incompatible, another barrier to sharing data.
The challenge is to level the playing field so different departments and functions across the factory can communicate with each other.
The starting point is to establish a basic IT infrastructure and architecture to capture that precious data. This will inform future projects: data analysis and integrating the supply chain.
Colin said: “We’ve got the equipment - the machinery to make things happen - now we want to take that first step to create the backbone – the architecture - to capture and monitor and analyse the data our equipment produces.”
Using matched-funding from Made Smarter LWS is preparing to install that ‘backbone’ – the physical architecture which will bring that data to life.
That starts with a new server capable of supporting the current and future scale, processing capability and all-round performance.
Then there are wireless technologies for data transfer and finally, a cloud solution for storage to allow secure backup and the capacity to integrate with the supply chain.
Migrating the business to the most up-to-date software is also an important part of the project.
“We have software of a variety of ages which is incompatible with other software in the same work process,” Colin said. “Our aim is that everyone in the business is on same platform operating on the most advanced system that marries with the advanced equipment in the factory. That way we can harness the power of data collection and start the process of refining energy consumption saving, waste reduction and potential increase in sales - the three drivers for this project.”
This first phase is crucial to LWS’s ambitions of a full systems and data integration up and down its supply chain.
LWS believes system and data integration will ultimately allow it to manufacture more prepared salad using less energy and producing with less waste.
Energy savings can be made by detailed monitoring of the data from sensors within the motors, water system and air system, which will enable the business to adjust and refine systems to reduce consumption by 2% within three years – reducing its energy bill by £25,000 per year.
LWS says the new capability of recovering, analysing and monitoring data sensors and key performance indicators of the processing equipment will cut the waste produced from raw salad products by 2%.
By improving the efficiency of the factory operation, the business forecasts a direct increase in productivity, boosting sales by 0.5% by 2022.
It is also forecast that GVA increase to the region will be £3.2M by 2022.
The design of the new bagged salad factory gives LWS considerable room to expand.
By installing the critical systems architecture now, it enables that growth, increases the capacity to dig deeper into the data to find even more efficiencies, and allows LWS to integrate into its 17-strong grower supply chain.
Colin explained: “What we ultimately want is to be have access to real time harvesting data from the fields in terms of how much salad produce is being picked and how quickly. This will help the factory ensure customers’ orders are met to specification, quality and delivery time.”