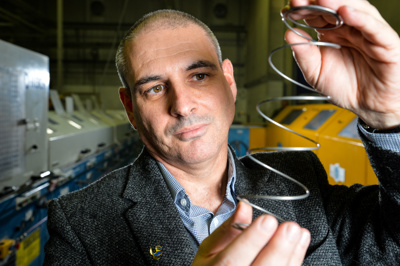
A spring manufacturer has unlocked and accelerated productivity, net zero and innovation gains with the support of industrial automation specialists.
Harrison Spinks Products (Spinks), a leading UK spring component manufacturer based in Leeds, collaborated with Bespoke Automation Controls Solutions (BACS) also based in Leeds, and the Manufacturing Technology Centre (MTC) on a collaborative R&D project through Made Smarter Innovation.
Innovation Case Study - Spinks and BACSThe solution - which leverages IIOT technologies, networking, machine learning and analytics - has digitised and automated a traditional analogue process which has remained relatively unchanged for decades.
Tests on two production lines demonstrated an increase in OEE of 25%, reduced waste by 56% and slashed energy use by 4%.
The project has been transformative for Spinks and accelerated plans to roll out the solution across other lines.
Chris Needham, Innovation Lead for Made Smarter Innovation, said: “Creating and adopting the latest in digital technology solutions will be key to drive energy efficiency, productivity and growth across manufacturing industries.
“It has been great to see how these very traditional engineering processes have been able to explore data-driven solutions and make such a large step reduction in waste material plus energy reductions. It demonstrates the varied reach that digital can have and how this type of success can be replicated in many other engineering settings throughout the UK and beyond.”
The Inspiration
In its request manufacturing innovation Spinks is also an OEM, designing and building more efficient and sustainable machines that it uses in its processes.
To manufacture its micro coils for mattresses, Spinks uses wire drawing, a traditional process which reduces a wire’s diameter and increases its length by threading and pulling wire through dies, using motorised drawing blocks.
Spinks has six lines which cold draw 5.5mm high carbon steel rod to wire with a diameter of between 0.67 and 2mm. 0.67mm, the finest wire available in the mattress spring industry.
However, the current manual process is inefficient and quality issues aren’t discovered until the end, resulting in unnecessary high levels of scrap metal and wasted energy.
Spinks, BACS and the MTC came together to try and overcome these challenges.
The Innovation
To start, the MTC used process mapping and sensor selection to identify the opportunities for process control, monitoring and the application of digital solutions.
The MTC then built computational fluid dynamics models to understand the thermal behaviour of the wire drawing line, the efficiency of the cooling system and energy consumption. Lifecycle analysis modelling provided insight into the environmental impact of the wire drawing processes, the materials used, and opportunities to explore sustainable wire manufacturing and waste reduction. Meanwhile, die wear analysis modelling used different techniques to study the wear profile of the drawing dies and improve changeover frequency and efficient die use.
Sensors were then installed to provide data points for process understanding and optimisation.
BACS’ role was to manage the entire software architecture design and code development, along with the design and implementation of the supporting database. Additionally, the team developed and installed the network architecture, dashboards, HMI systems, PLC code, and handled protocol conversion.
The solution involved installing six bespoke electrical control panels and 68 sensors. Meanwhile, Raspberry Pi devices were used as edge devices for dashboards and data collection, achieving over 800 data points and managing 238 I/O points. The project also included the installation of 37 current clamps, seven dashboards, a local server, a cloud server and three IoT gateways.
These measures captured previously ‘invisible’ data, including temperature, water flow, ovality, and alignment (or offset) of the tooling, as well as torque and power draw.
James Hooton, Director of BACS, said: “Our bespoke solution created a smart network of digital decision tools allowing Spinks to simulate and predict resource and energy use, assess production and improve its effectiveness.
“Visualisation has been introduced from shop floor to top floor, with an HMI on the line and a cloud-based dashboard for remote monitoring via iPad. The platform is also integrated with Spinks’ ERP system, meaning the leadership team is also able to access and analyse the performance data to identify trends, giving the ability to be able to scrutinise batch data to identify any issues with wire quality.
“The solution has transitioned a customer’s wire drawing process into the digital space.”
The Impact
Access to vast amounts of previously ‘invisible’ data and introducing analytics into the real-time and post-production processes has been transformative for Spinks.
Analytics also means the Spinks can identify issues quickly and with more accuracy, reducing any downtime of machines, and reducing bottlenecks to the onward spring coiling process.
Across the two lines involved in the project, OEE has been increased by 25%.
Process parameter improvements means that Spinks has reduced the number of die changeovers by 75% - from two per week to once every two weeks - and increased the amount of wire produced per die by 60%. On top of this the amount of time it takes to replace die sets is down by 33%, the equivalent of an hour for an 11 block machine, and 30 mins for a five block machine.
The ability to react to issues and the accuracy of the process has reduced the amount of scrap waste by 56%.
Spinks has reduced the energy required to actually pull the wire through the die by 4.3% with potential to reach 25% with refined monitoring.
Visualisation means the leadership team is able to access and analyse the performance data to identify trends and scrutinise batch data to identify any issues with wire quality.
Richard Essery, Director of Sustainability and Innovation at Spinks, said: “Wire drawing is a very traditional industry. This project has automated a very manual, inefficient process, and freed up our very capable engineers to focus on more high value tasks.
“Our ambition was a greater level of control of the process and analysing data to drive improvements. The results have been extraordinary. I’ve been doing this for 40 years and have seen innovation throughout the business, but I am genuinely excited about the impact this will have on our wire manufacturing and the opportunities it will have for innovation in products, process and machinery.”
Another outcome of the collaboration with the MTC is the ongoing development of a prototype demonstrator of the wire-drawing line, which, when complete, will enable Spinks to use for training and the MTC to engage with industry as best-practice.