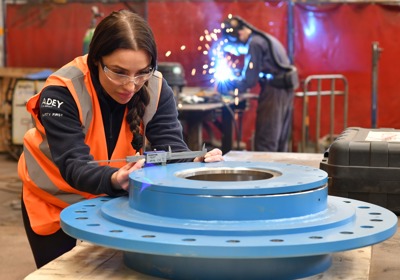
SME manufacturers are experiencing productivity and net zero gains after deploying manufacturing analytics software through Made Smarter Innovation’ Smart Manufacturing Data Hub (SMDH).
The 25 companies have partnered with Output Industries, a software start-up based in Cornwall, one of 12 Lighthouse Projects, funded by SMDH to develop a market ready solution for deployment and dissemination to SMEs.
Innovation Case Study - Output IndustriesBy connecting their operations to Output Industries' Busroot platform, manufacturers are able to make data-led decisions to enhance operational and energy efficiency, and drive a culture of performance. Early results suggest productivity gains of between 10 and 15%.
Collective insights from manufacturers working in 36 Industry sectors have so far led to a 28% reduction in energy costs and 30% reduction in co2 emissions.
Sonya Coleman, Programme Director for MSI’s Smart Manufacturing Data Hub, said: “Lighthouse Projects like Output Industries have enabled SMEs to embark on a smart manufacturing journey, de-risking major investment, yet enabling growth. Simultaneously, the data is being leveraged to benefit the wider sector.”
Chris Needham, Innovation Lead for Made Smarter Innovation, said: “As we embrace the digital manufacturing revolution, it is important SME manufacturers across the UK capitalise on the productivity and growth gains, and the opportunity to make more sustainably, that comes with adopting the latest data-led digital technologies.”
The Inspiration
Manufacturers are amid a data-driven revolution. With access to real-time production data, they can become more efficient, productive and sustainable.
But many SMEs lack the resources and know-how to deploy data capture technology and combine the different data sources into one cohesive view. It is also common for a company to have a vast array of machine types with varying brands, ages and compatibilities.
Recognising the value of data inside an organisation is important, but so is sharing that data with others. More sophisticated analysis and application of manufacturing data requires collaboration and the creation of a data ecosystem.
The SMDH was created to kick start that ecosystem among SME manufacturers, offering 12 technology providers the chance to demonstrate the impact of adopting low-cost digital solutions into their operations.
The Innovation
Through the project, Output Industries has developed and launched Busroot, a complete manufacturing analytics platform that provides accurate, real-time information regarding the status of all machines, processes, and production via an easy-to-use web interface accessible on any device.
The platform leverages cloud computing and open-source IoT devices to enable SME manufacturers to understand what is happening inside their factories.
By blending real-time IOT data and broader manufacturing master data, the Busroot platform is able to provide accurate, real-time data on manufacturing operations.
So far Output Industries has rolled out the solution to 23 of the 25 companies in sectors including machinery, food and drink, textiles, medical devices and plastics.
From day one, these manufacturing organisation have been given access to core manufacturing KPI’s including Overall Equipment Effectiveness (OEE), cycle time analysis, production output, yield rates, downtime analysis, labour efficiency, waste and scrappage, and energy inputs.
The data is then shared with the MDEP, via the Busroot platform, where data scientists have provided data analytics, data analytics tools, and benchmarking insight.
Gabriel Kissin, Data Scientist at SMDH Consortium member, said: “Machine time can be broken down into different fractions, including productive/unproductive time, issue/no issue time, and so on.
“The Output Industries dataset is a valuable resource for understanding machine efficiency by visualising total time in each of those fractions, for each machine. Looking at the total proportion of time in each fraction allows manufacturers to easily identify which machines are most productive, and where there is potential for efficiency gains. Finally, looking at rolling proportions over time indicate utilisation rates at specific times of the day/week, enabling manufacturers to drill down to the exact times when those efficiency gains can be realised.”
The Impact
So far Output Industries has rolled out the solution to 23 of the 25 companies in sectors including machinery, food and drink, textiles, medical devices and plastics.
While different users are at different stages of deployment, early tests are demonstrating striking outcomes.
One company, a manufacturer of heavy machinery, has reported an 11% increase in productivity after monitoring machine downtime and improving asset utilisation.
Another, Adey Steel, based in Loughborough, is trialling the Busroot platform across multiple CNC machines, and has experienced an increase in productivity and efficiency in a key area of their manufacturing process.
Richard Greasley, Group Production Director at Adey Steel, said: “Using the insights we gain from Busroot, we have identified areas for improvement in efficiency and productivity. Our next step is to integrate energy monitoring, which will provide further insights into our production operations and assist us in achieving our net zero goals in 2025 and beyond."
Output Industries is forecasting productivity increases of between 10 and 15% across all 25 companies.
Mike Wright, Co-Founder and CEO, said: “A machine is only valuable to the manufacturer when it's doing what it should be doing. Our platform helps identify which machines are not working and why, enabling a manufacturer to make changes to reduce waste, increase the utilisation of those assets and increase productivity. By being more efficient, you're going to do more with the same, if not less, and see increased revenues.”
Manufacturers are also beginning to collect the energy consumption of those machines or stations, and use Busroot to understand and benchmark consumption, as well as correlate that to production.
Mike added: “These insights empower manufacturing SMEs to be more efficient, productive, and profitable. identify real-time per-unit energy inefficiencies, lowering operational costs and environmental impact.”
“Our solution offers a rapid, cost effective, low-disruption adoption process which gives manufacturers confidence to scale.”
Feedback from the project is helping Output Industries further develop Busroot to ensure it meets the changing demands of end users. The project has enabled the business to expand its team by 33% to target growth by retaining manufacturers using Busroot software through the project, and new business.
Cara Roberts, Business Development Manager at SMDH, said: “Output Industries has been a real success story. By collecting and anonymising a variety of different data sets our analytics team are now merging it with other Lighthouse projects to create valuable industry benchmarks.
“By the end of the programme we are confident that we will have created a trusted environment where manufacturers share their data safely, gaining value for their own businesses, while supporting UK manufacturing.”