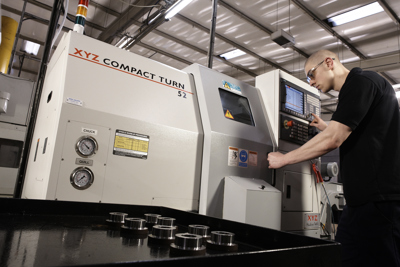
An engineering company, supported by Made Smarter, has embarked on a mission to create a digitally integrated factory to drive growth and productivity, and penetrate new markets.
For 55 years Mini Gears (MG), based in Stockport, has built a solid reputation as a manufacturer and supplier of high-quality machined parts, gears, and gear racks for a variety of industries including aerospace, oil and gas, and nuclear and defence.
It has recognised the need to embrace new digital tools and technologies to speed up its internal processes, safeguard its future and tap into new markets, including rail.
Using Made Smarter’s digital transformation workshops, MG has developed a roadmap tailored to its needs.
Further support has so far enabled MG to upgrade its IT systems and lay the foundations for a major data and systems integration project which will ultimately integrate all of its CNC machines through upgraded ERP and MRP systems.
Full implementation, which has been delayed by Covid-19, is expected to be completed by the end of the year, and is forecast to contribute towards substantial improvements in productivity, efficiency, cost control, quality and planning.
Case study - Mini GearsMade Smarter’s support in creating our digital strategy and getting this project off the ground has been invaluable and accelerated our approach by years.
This project will be the first significant industry 4.0 step in achieving MG’s goal of a paperless factory and drive growth and productivity.
The upgraded systems will make us more efficient, which is essential to be competitive in the automotive, aerospace, oil and gas, and medical industries, and to penetrate the rail industry.
Peter Durkin, Managing Director of Mini Gears
MG employs 90 staff at its 35,000 sq ft manufacturing site and produces parts for customers in the UK and worldwide.
While it has invested in new technology to produce high quality components, its systems are disparate and unconnected.
A key challenge is the communication of scheduling and dissemination of drawing amendments to the shop-floor.
Peter explained: “Currently every part we manufacture generates an amount of paperwork that has to be printed, collated and issued with the job. This is time consuming and is further exacerbated with customer changes during manufacture as all paperwork has to be retrieved from the factory floor, amended and reissued.
“To put this into perspective, Mini Gears manufactures on a subcontract basis 135,000 parts per month with 175 different variants. We have over 100 machines in our machining capacity and need real time data on the status of all jobs in production to maximise our efficiencies.”
Prior to the disruption caused by the pandemic MG upgraded its IT moving all PCs to Windows 10 and Office 365, and installed new digital cabling throughout the factory.
The data and systems integration project will ultimately integrate all 39 of its CNC machines through new bespoke ERP and MRP systems.
Other proposals include upgrading some machines to CNC operation and the adoption of RFID technology for materials control and employee attendance monitoring.
Peter said: “The new technology means all our manufacturing machines will be fitted with a touchscreen enabling job process cards to be issued and updated electronically.
“All documentation relating to the job including drawings, quality documents and information videos can be viewed on the screen, eliminating paperwork.
“Operators will clock on and off jobs at the machine thus providing better data capture enabling us to react to customer changes more efficiently and provide real time capacity information.”
Upgrading to Microsoft 365 has given MG its first taste of the benefits of cloud computing.
Having the entire business on the same platform has introduced streamlined collaboration tools, IT setup and management, and sped up data sharing and access between different business operations, its customers and supply chain.
The workforce can now access vital data remotely in real-time, increasing productivity.
The most significant benefits will come from the new system integration project which allow MG to collect valuable, reliable and accurate data from its machines’ performances, giving MG visibility and control over production. This data can then be seamlessly integrated into its IT platform. This is forecast to contribute towards substantial improvements in productivity, efficiency, cost control, quality and planning.
Peter said: “To have oversight over the entire factory will be transformational. We will be able to identify problems and capitalise on opportunities much more quickly.
“By using touchscreen displays at machines job process cards including drawings, quality documents and information videos can be issued and updated electronically, eliminating paperwork, and enabling a much more efficient process.
“The digital processes automate things such as scheduling, stock control, improved production and capacity planning alleviating MG’s time, which can be redeployed for more specialised work.”
Better control of capacity planning time will enable MG to give customers more assurance on lead times, therefore enhancing customer experience.
The introduction of digital processes is a significant step towards MG’s ambitions for a paperless factory, greener practice, and a reduced carbon footprint.
Access to new data will help MG’s plan deliveries, preventing errors and reducing wasted or duplicate journeys.
MG’s workforce is fully onboard with the ambitions of the digitalisation strategy.
“At least 25% of the team at Mini Gears have been here for 15 years or more, which says a lot about how we approach our work and treat our staff,” Peter explained. “The years of experience and expertise creates a vital mentoring culture for new staff, which we anticipate will be reversed as we bring on board new tech savvy additions to the team.”
MG’s ambition is to invest in upgrading its legacy machinery into new state of the art CNC machines which will massively improve production performance and reliability, and integrate with the new system.
“With increased capacity comes a requirement to invest in new technology,” Peter said. “In the subcontract market, moving with the times is a must. It is critical to grow the business enough to reinvest in technology.
“We strive to become more than a subcontractor by providing a full comprehensive service to our customers. Digitalisation will help us achieve that goal and Made Smarter has been a valuable partner.”