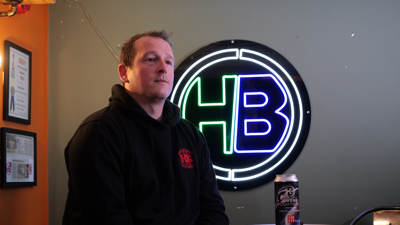
A West Yorkshire brewery doubles efficiency and improves product quality with support from Made Smarter
Horsforth Brewery, a West Yorkshire-based brewery has transformed its production process, improving efficiency, reducing manual labour, and ensuring consistent product quality by investing in a state-of-the-art canning machine. The project was made possible with support from Made Smarter Yorkshire & Humber, delivered by Oxford Innovation Advice.
Founded seven years ago, Horsforth Brewery produces a range of beers in cask, keg, and can for distribution across Yorkshire. As demand for their products grew, the business faced challenges with its existing canning process.
The manual canning machine in place required two staff members to operate it and was only capable of producing 200 cans per hour. Production was slow, labour-intensive, and prone to inconsistencies in quality, as the process relied heavily on the operator’s skill.
“The problem Made Smarter helped identify was the amount of labour that we needed,” said Mark Costello, Founder and Owner. “Our old canning machine was quite labour intensive with a manual process, loading the cans on and off again. And it all depended on the ability of the operator.”
The lack of consistency in canning also created issues with product shelf life. To ensure quality, the brewery limited the shelf life on its canned products to six months, which in turn limited its ability to supply more customers.
Despite recognising the need to upgrade to an automated canning solution, the brewery did not have the funds to purchase new equipment outright. This limitation became a significant barrier to growth, prompting the brewery to seek external support.
The brewery approached Made Smarter Yorkshire & Humber for help and was connected with Jeremy Boye, a Digital Manufacturing Adviser. As part of the Made Smarter process, Jeremy visited the site to assess the brewery’s operations, challenges, and opportunities for improvement.
“I met Mark in early spring. I came to see him, discuss the business’ challenges and get a good understanding of his frustrations within the business. We felt that there was potential in upscaling and growing the business, but some of the equipment in place was perhaps holding that back,” said Jeremy. “We looked at ways in which Made Smarter could help with consultancy support around digitisation and also capital support in terms of investing in new machinery.”
Made Smarter worked with the brewery to identify the need for automation in its canning line, offering consultancy support and guiding them through the grant application process. The brewery secured matched funding to invest in a modern, automated canning machine.
The new system automates key steps in the canning process, including loading, filling, and sealing the cans. This eliminates the reliance on manual labour, ensures greater consistency in the final product, and significantly increases production speed.
The results of the investment have been transformational for the brewery. Production capacity has increased by 150%, rising from 200 cans per hour to 500 cans per hour. Importantly, the new system only requires one person to operate it, compared to the two staff members needed previously. This has freed up resources, enabling staff to focus on other areas of the business and increasing overall productivity.
Automation has also resolved the issues with product quality and consistency. The new canning process delivers a reliable, high-quality product every time, allowing the brewery to confidently extend the shelf life of its canned beers from six months to nine months. This improvement gives the business greater flexibility when managing stock and increases the appeal of its products to a wider range of customers.
By increasing efficiency and improving output, the brewery has been able to meet growing demand and expand its customer base. It now supplies more local bars, restaurants, and retailers across Yorkshire, building on its reputation within the region and opening up new opportunities for growth.
With its production processes now optimised, the brewery is in a strong position to scale the business further. The increased capacity and improved quality means it can take on larger orders, develop new products, and grow its distribution network.
The success of this project has also highlighted the value of adopting digital technologies to improve operations. The brewery now has a strong foundation on which to build further improvements, with plans to continue exploring opportunities for automation and digitisation in the future.
Reflecting on the support received, Mark said, “I would definitely recommend Made Smarter. We wouldn’t be anywhere near where we are as a business without that new canning machine. So if anyone’s thinking about it, I definitely recommend getting in touch with them.”
Jeremy Boye, Digital Manufacturing Adviser at Made Smarter Yorkshire & Humber, added, “The brewery’s journey is a fantastic example of how automation can transform operations. By reducing manual effort and improving quality, they’ve created a more efficient and scalable process that will support their productivity and growth for years to come.”