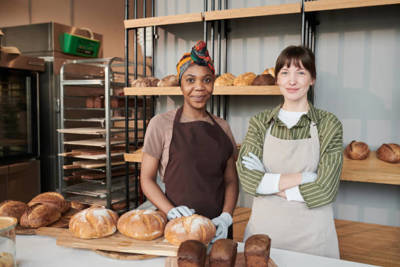
Bakery manufacturing is on the rise across the UK. Bakeries – by which we mean large-scale cake and brownie producers as well as those who supply wholesale and smaller, niche family businesses – are turning to new technologies to successfully compete.
Not only do these digital tools drive efficiencies, but they also boost staff morale and bolster brand reputation due to added compliance and traceability – something that has become even more important since Natasha’s Law came into effect on 1st October 2021.
Read on to learn about the government support available for bakeries small and large, as well as our advice to baked goods manufacturers heading into the next 12 months.
ERP platforms
Enterprise resource planning (ERP) systems are a configurable engineering solution, meaning they’re developed to fit each unique company. An ERP platform has various modules which relate to each business area (such as finance/accounting, supply chain management, human resources, manufacturing and logistics, and customer relationship management) and are rolled out in stages as the database is being built. This paves the way for more accurate data tracking and management, making compliance easier to prove. They can also ensure your precise specifications (such as the recipes you use) are met with each batch, helping to regulate batches and maintain high standards.
But the benefits of ERP systems go far beyond this. For example, given the cost-of-living crisis, there are only so many rising fees that bakeries can pass on to the consumer – this presents a need to improve accuracy and reduce waste. An ERP platform plays a role in this, helping to cut down on inventory inefficiencies by enabling you to order components when needed, and produce and ship in good time – rather than keep items waiting around. And this works well whether you mass-produce batch items or manufacture to-order products.
Process control technology
Process control technologies go hand in hand with ERP systems and can ensure compliance as well as better team communication and collaboration. First, you’ll need to review your operating procedures to:
- Make sure your team is given the right direction and can follow the standards
- Assess how lean your process is, and implement changes before moving forward with technology
- Provide your staff with examples of how work needs to progress at each step
Once integrated within your organisation, process control technology can monitor and control manufacturing processes. Sensors measure and adjust the conditions that a product is made under, and the technology sends that data to other systems where you can analyse performance, plan more efficient workflows, and audit activity. You’ll be able to store these records in the form of batch and shift reports, or you can also create personalised reports and use this to capture employee knowledge.
Process control technology can therefore help food manufacturers pinpoint exactly where each ingredient has come from to easily validate that it meets quality specifications and can be certified as, say, vegan or gluten-free. Additionally, these tools can be used to identify which stock needs to be used first (like short shelf-life ingredients), reducing waste and costs.
This level of oversight often results in the likes of high speed and productivity too. Plus, it can hit the brakes when the process is about to go wrong, giving your teams the opportunity to proactively make amends.
Robotics and automation technology
The main way in which robotics and automation can support compliance is through accuracy. They can be used to precisely weigh and dispense ingredients, and cut the finished product to size. ‘Brownies in a box’ products are a great example of this in action – and show how your staff can benefit too. These postal treats have skyrocketed in popularity, but the cutting of dense products can trigger repetitive strain injury as well as sore muscles and joints.
An automated cutter takes the task off their hands, reducing the likelihood of human error and potential injury. Plus, staff can then be relocated to higher value business areas, where their roles are more varied and satisfying.These technologies are also equipped with data collection systems. So, at the same time as they’re helping drive the manufacturing process itself and removing onerous or heavy tasks away from people, they’re also feeding your organisation with operational data. Once again, the analysis of this data can provide business intelligence which can be turned into process improvements as well as better compliance practices.
If you’d like to see robotics in practice, take a look at Bells of Lazonby’s case study – they adopted an ultrasonic cutting robot to increase accuracy and save time, amongst many other positive business outcomes. And if you’re unsure about robotics or how much this technology would cost your business, we have in-house advisers that would be happy to help…
Start improving compliance and traceability today
We’ve mentioned just a few applications of technology in this piece, but there are many more you can explore. Whether you’re a startup in the space or a heritage business, there are countless tools that can help improve traceability and compliance within your organisation – as well as unlock a whole host of other benefits.
What’s more, you could be eligible for a government grant if you bake or manufacture food in the UK and have fewer than 250 employees.
If you’d like to know more about the solutions you could implement to achieve your business goals, get in touch with our team at Made Smarter today.