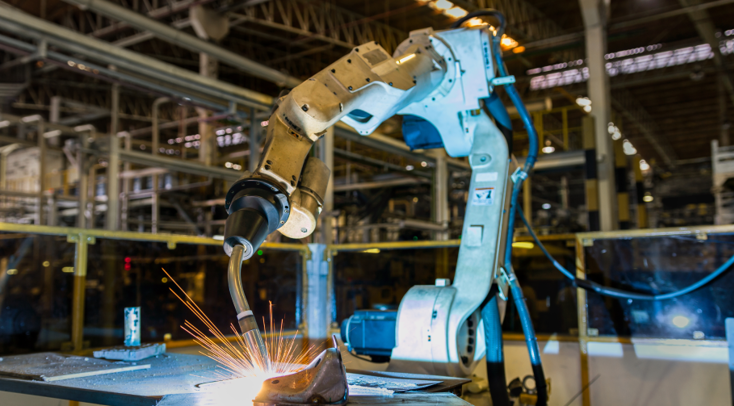
Introduction
While Automation has come to mean the use of robotics and machines to reduce or replace work previously done by human workers in the manufacturing process, robotics is only one aspect of how manufacturing automation works.
Automation is any type of machine or device used to perform a process without, or with reduced, intervention from a person.
Robotics is a type of automation which involves the use of a machine, usually, a mechanical arm, which can move in three.
or more directions, that can be used to complete material handling and pick-and-place tasks faster and more efficiently than manpower alone.
The introduction of automation often improves productivity by allowing staff to focus on more complex, higher value-add, or more intricate and interesting tasks. Other benefits of automation include improved health and safety, increased material utilisation, higher quality products, reduced cycle times and reduced lead times.
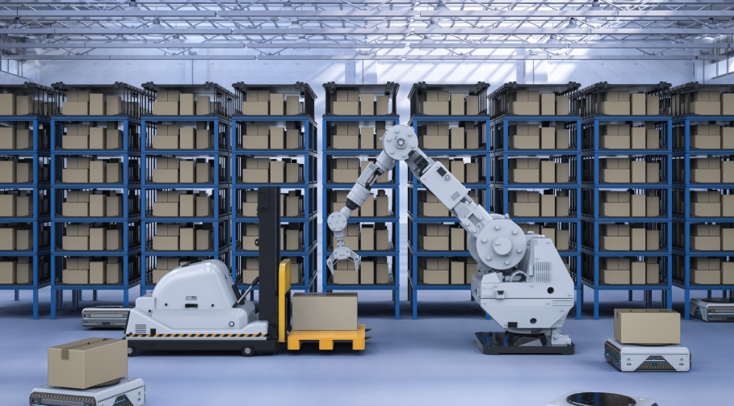
Collaborative robots or industrial robots?
Cobots also don’t require extensive experience to program and are flexible, allowing them to be quickly moved and repurposed for a different task.
Industrial robots are used for tasks requiring higher speed, heavier tools or products, or in harsher environments. Industrial robots require safety cages and often need specialist programming skills. If you think about the robots used for welding, assembling, or painting cars on a production line, these are industrial robots.
While useful, automation and robotics may not be the right solution for every manufacturing process or production line. Low-volume or delicate production process would not be suitable for a robotics solution.
Made Smarter can help your manufacturing business to define problems and find a solution that suits them. Once a solution has been determined, our advisor’s team can help you access grant funding as well as provide ongoing help and support.