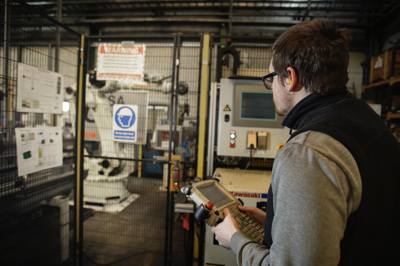
A manufacturer of aluminium components has unlocked opportunities to reduce emissions and boost productivity and profits through data analytics and visualisation.
Ryobi Aluminium Casting, based in Carrickfergus, Northern Ireland, partnered with Made Smarter Innovation’s Smart Manufacturing Data Hub (SMDH) to utilise its cloud-based platform. This allowed the business to upload and analyse factory and energy data for unique insights.
Innovation Case Study - RyobiRyobi’s is also part of the Manufacturing Data Exchange Platform (MDEP), a data mutual where anonymised data is shared with the wider manufacturing ecosystem, academia and technology to extract insights, explore appropriate solutions and identify wider trends.
Simon Coward, Programme Director for SMDH, said: “We have worked closely with Ryobi to develop their data acquisition, interrogation techniques and technical support to implement a new adoption-ready innovation.
“Ryobi is now able to capture data from multiple sources for simultaneous analysis to provide novel production insights. Our partnership has established a way to access gradual insights from multiple data sources and developed a reusable computing model. Ryobi can scale this process, and receive key insights and KPIs from an extremely high volume of data within their factory.
“This has led to enhanced machinery performance, downtime reduction and energy efficiency with reductions in carbon emissions. In turn this will allow them to focus on innovative ways to optimise their manufacturing processes and energy usage.”
Chris Needham, Innovation Lead for Made Smarter Innovation, said: “Made Smarter provides the opportunity for innovative collaboration that will be transformative in driving industry competitiveness.
“This project is a great example of what can be achieved by giving businesses access to expert guidance and digital solutions.”
The Inspiration
Ryobi Aluminium Casting, based in Carrickfergus, Northern Ireland, produces aluminium components for the automotive industry using a high pressure, energy intensive die casting process.
While it has its own goals to reduce its environmental impact including achieving carbon neutrality by 2050, the business is also under pressure from customers such as Volkswagen and Jaguar Land Rover, as well as its broader supply chain.
While Ryobi is certified to ISO 14001, the internationally agreed standard for an environmental management system, and uses submeters to measure the energy consumption of production equipment, such as die cast machines, this data was not being analysed and reported.
The business realised that to achieve its ambitious CO2 emissions and waste reduction goals, it needed to commit to a new approach for how it captures, analyses and visualises its data, alongside other critical business information, such as production outputs.
Ciarán Maxwell, Low Carbon Project Lead for Ryobi, said: “There is an extraordinary amount of data within our factories that has the potential to identify value insights which could not only save us time, money and energy, but unlock innovation in how we design and manufacture.
“While we have taken some steps to capture the data, the previous database and platform wasn’t easy to use and was essentially obsolete. We needed a one stop shop for all our data, a modern, bespoke digital tool where we could visualise the opportunities to be more efficient, profitable and environmentally responsible.”
The Innovation
Ryobi undertook a project with the Smart Manufacturing Data Hub in partnership with Manufacturing NI and the Energy Systems Catapult to develop a dashboard that would combine data from Ryobi’s electricity sub-meters for two different die cast machines with production output and Overall Equipment Effectiveness (OEE) data for the same machines.
Additionally, granular tariff data was added to the analysis to allow Ryobi to analyse how the variable cost of electricity impacted on its production cost.
The data analysed was summarised daily, weekly, and monthly to provide both low-level insights and a higher-level summary to demonstrate longer-term trends.
Data from two different die cast machines, which had made the same parts during the three month observation period, were included in the analysis to allow a comparison of different equipment.
The dashboard also provided a functionality to compare production and energy consumption
KPIs between specific days with more granular insights about the energy consumption profile for either day.
This allowed the user to compare days with very good performance alongside those with poorer performance, and identify potential root causes of inefficient energy use or increased energy costs.
The Impact
While the team continues to analyse the outputs from the project, it has demonstrated some clear insights.
For instance, data from two die-casting machines revealed that one was 13% more energy efficient and demonstrated an 11% higher OEE than the other. Understanding the ‘how’ and ‘why’ has the potential to unlock thousands of pounds a year in savings, and achieve a considerable reduction in emissions.
The success of the prototype has given Ryobi a vital benchmark of production and energy consumption data and the confidence to invest in a new bespoke platform with automated data exchange and real-time visualisation.
Maxwell said: “We are committed to a data-led approach to decision-making. That requires connectivity, automation and data analysis.
“In our business a 1% saving in energy use is considerable in terms of the bottom line and supporting our net zero journey. This project has unlocked some truly striking insights comparing just two of our machines.
“If we add the additional 22 machines in our factory, we could have a data platform which enables us to schedule our production more efficiently, price our products more accurately and competitively, and become more profitable and environmentally responsible.”
Ryobi is now moving to phase two, implementing a new database during 2024.
“Once the platform is up and running we are expecting to reduce our overall energy consumption by up to 20% in the first year,” Maxwell added. “For an energy intensive business like ours, that would be huge. It will unlock capital to invest in renewable technologies and chase reduced energy consumption and spend further.”