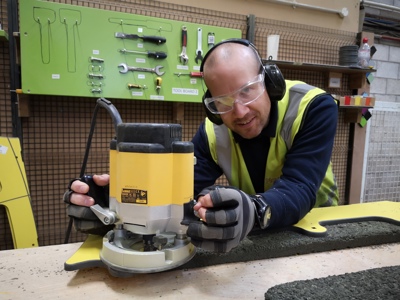
A Cumbrian playground equipment manufacturer aims to double its global exports by investing in a Smart CNC machine, following specialist digitalisation advice from Made Smarter.
Playdale Playgrounds designs and makes apparatus for councils, schools and leisure attractions and has produced 23,000 play areas in 49 countries to date.
But the sector is incredibly competitive, prompting Playdale to embark on an ambitious plan to become a fully digital factory.
Case Study - Playdale PlaygroundsWe have been looking at our digital strategy for the last few years, but now with the help of Made Smarter, we can accelerate our plans.
Paul Mallinson, Technical and Operations Director, Playdale Playgrounds.
Over the past 40 years, Playdale has grown to achieve a £12M turnover with 100 staff working across two factories and a distribution warehouse.
The forward-thinking SME has spent the last two years developing a digital roadmap, adopting lean manufacturing principles and investing in IT infrastructure.
It is now ready to apply advanced technologies to key processes such as the design and manufacture of wooden components.
Paul explained: “As it stands the components are created using 3D design software and arranged in optimum position using nesting software. However, it takes around two days to programme our current CNC machine to schedule and cut around 500 panels. The current process is very disjointed, and there is too much manual intervention. We need to do much more - and quicker.”
Playdale also intends to find improvements by extracting and analysing production data from legacy equipment such as saws, drills and presses.
Playdale has invested in a Smart CNC machine which will integrate with the CAD and nesting software, and the ERP system.
The inbuilt sensors of the machine and the associated software will allow the business to capture, monitor and analyse data in real-time.
For the pilot project focussing on legacy machinery, sensors will be attached to the drill and connect to a Brainbox system which captures and processes the data for display on digital screens.
The integration of the design and manufacture processes will allow Playdale to achieve significant improvements in efficiency, output, productivity, reduce material use, tooling and downtime, and improve quality.
The combined benefits are forecast to save the business £40,000 per year.
Paul said: “While this Smart CNC machine will generate huge productivity gains, efficiencies and savings, hidden gains will be reaped from the analysis of the data captured from the operation of the work cell itself.
“The implementation of predictive maintenance through the embedded sensors will reduce the downtime of our machines.”
The new system will reduce production time by 20%, offering the new capacity to broaden its product portfolio and customise.
The Smart CNC machine will allow Playdale to focus on growing exports from £1.7M to £3M within three years.
“Our export growth has put greater pressure on our ability to manufacture in shorter timeframes and pressure on margins due to the competitive global market,” Paul said. “Digitalisation will mean that we can protect and even increase our margins, while being more competitive and deliver excellent customer service to boot.”
By capturing data from legacy machinery, Playdale will be able to fully understand how it uses its equipment and the impact of that use, creating four new jobs and upskilling the workforce.
The project is expected to contribute an additional £1M to the region’s GVA over the next three years.
Other projects on the horizon include additive manufacturing for rapid prototyping, using 3D laser scanners for site surveys and VR and AR technologies to evaluate new designs for customer engagement.
Paul said: “These two projects will create a step-change towards our future state and pave the way for the integration of the remainder of our work production cells, in addition to the creation of totally digital workflow from initial enquiries through to delivery, installation, customer acceptance and on-going support. It’s an exciting time for Playdale.”