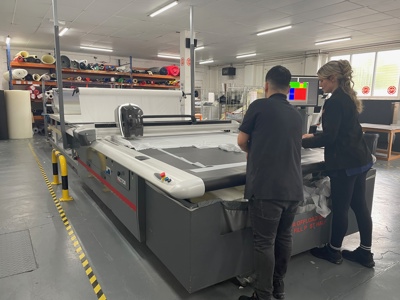
Openhouse Products is a leading UK textiles manufacturer for the emergency services and health sectors.
The business, based in Birkenhead, supplies a large range of custom bags, medical equipment and consumables to NHS Trusts across the country.
Thanks to a grant from Made Smarter the business has implemented a new cutting machine which is 10x faster than the previous technology.
Case Study - Openhouse ProductsOpenhouse Products had already been on quite an innovation journey since it was established in 1992.
The business was delivering a large order for laptop carriers when a chance conversation with one of the seamstress’s husbands, who worked in the emergency services, changed the course of their history.
They pivoted their product after realising what a challenge it was for paramedics to keep track of all their kit and find each piece of equipment during an emergency.
Within two days a prototype had been made and the business started specialising in manufacturing textile products for the emergency services.
Since then, the company has grown steadily over the years, even developing their own material, micrAgard, for the bags which set a new standard in infection control.
However, there was a bottleneck in the manufacturing process at Openhouse Products.
Head of Manufacturing Josh Reid explains: “We had 14 full-time machinists, but the cutting process was lagging behind.
“The business was using two old Gerben Paragon DCS2500 machines which, by this point, were 16+ years old and held together by tape.
“Cutting is just the start of our process, so the old machine with less capacity was holding up other areas and causing productivity issues down the line.
“We knew we didn’t just want to replace it like-for-like, so we decided to approach Made Smarter about alternative technology solutions and grant funding.”
A Digital Transformation Workshop was organised with a specialist technology advisor from Made Smarter who analysed the business’s product, process and people.
After mapping the manufacturing process and understanding their challenges, the advisor created a digital roadmap of what steps Openhouse Products could take to expediate digital transformation.
Made Smarter is a government-backed programme to help SME manufacturers adopt industrial digital technologies. There is a range of support available including: specialist technology advice, digital transformation and road-mapping workshops, funding opportunities and leadership and skills development and training.
Thanks to Made Smarter the business received a grant of £40,000 to help purchase a new A Lectra Vector IX cutting machine.
The Lectra Vector IX is a fully connected Industry 4.0 solution with embedded smart services which, via 120 in-built sensors, sends real-time data to Lectra’s International Advanced Technology Centre in Bordeaux, France. This ensures data is collected and analysed in real time, allowing predictive maintenance of the machinery to reduce downtime.
The new cutting machine also enables ERP system integration to help track the amount of raw material being used for each job and allows the business to accurately foresee the savings that will be achieved through economies of scale.
This includes time savings through the machine's ability to cut multiple layers of material, and cost savings through the machine’s auto nesting function which orientates the parts in the most efficient way.
Openhouse Products were part of the Made Smarter Pilot Programme in the North West. Grant funding is now capped at £20,000 per SME, as the national programme endeavours to help as many small to medium sized manufacturers in the regions as possible adopt digital technology.
Since installing the new cutting machine, it has had a very positive impact on Openhouse Products and the efficiency of its production line.
Josh said: “The new cutting machine is 10x faster than the ones we were previously using.
“The Vector IX is much more effective and includes predictive maintenance which means less downtime on the manufacturing line. It has solved the problem for us while eliminating production downtime.”
It also fits with the ethos of a business which has been innovation-led since its inception in 1992.
Josh added: “Our business has always been really hot on continuous improvement, so we are continually looking at ways to be more effective and efficient as a manufacturing business.”
Finally, it means Openhouse Products can better serve their clients and fulfil a greater number of orders for the NHS, as they already supply into most of the NHS Trusts including the North West and the London Ambulance Service.
Since investing in new technology, with the help of Made Smarter, Openhouse Products has geared up for even bigger growth with turnover and staff count growth.
Explaining that their strategy is to focus on exports, Josh added: “We are looking to grow our business further especially in regard to exports and setting up distributors overseas.
“We also intend to continuously improve our business across the board, driving efficiency and innovation whenever possible.”
The business has set up Openhouse Products Australia which is an exciting opportunity to supply into new geographical markets.