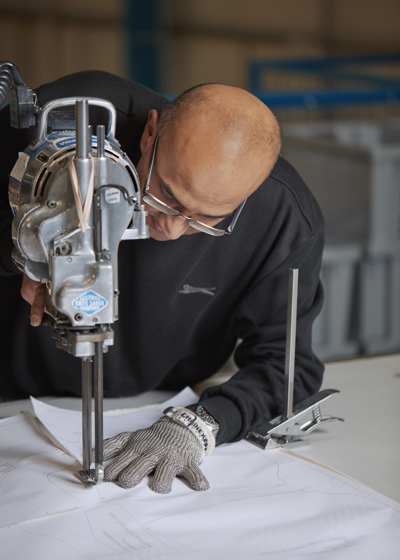
A heritage textile manufacturer, supported by Made Smarter, is aiming to increase productivity by 40% through a transformational data and systems integration project.
Over its 160 year history, Cookson & Clegg (C&C), based in Blackburn, has gone from producing leather products and manufacturing military apparel to premium brand clothing and protective wear such as medical scrubs, gowns and reusable face coverings.
When TV sewing expert and tailor Patrick Grant and his sister Victoria rescued the business from collapse in 2016 they recognised digital technology was the key to survival and growth.
Through Made Smarter’s digital transformation workshop C&C created a roadmap involving some key projects including adopting a digital workflow system, future phases of automation, and introducing a smart factory layout.
C&C is now embarking on a major data and systems project which will capture real-time data from every part of the production process and enable the leadership team to make informed decisions to identify efficiencies, generate more accurate pricing, and increase profitability.
The new system also aims to stimulate a cultural revolution within the business, improving the pay and job satisfaction of its skilled team machinists, a key part of its 40 strong workforce.
View the Case StudyWith the support and advice of Made Smarter we have been able to pursue our ambitions of improving both productivity and cost control across our operations by adopting digital technology.
Capturing data from the shop floor and being able to monitor it in real-time is an exciting first step on our digital transformation journey.
Patrick Grant, Managing Director of Cookson & Clegg
While C&C has invested in a broad range of semi-automated and manual equipment, its systems are disparate and rely on manual recording of production data for analysis.
That lack of transparency in the production lifecycle means that the leadership team is unable to accurately assess operations, production timings and costs to ensure that production is as efficient and profitable as possible.
Victoria said: “As a group of brands that has always supported the UK textile manufacturing industry, we acquired C&C because we believed it was a quality business with some extremely skilled employees. However, the traditional ways of doing things and embedded inefficiencies have held back the business from keeping up with the rapid changes in textile manufacturing.
“There is a lot of knowledge and experience in the workforce, but it is in their heads, and there is no hard data to back up decision making. Everything is recorded manually and there is little collaboration. It means that vital information like pricing and production planning can lack accuracy.
“The Made Smarter digital transformation workshop process helped us acknowledge that the shop floor was a black box and the first vital step for our business was to get hold of all that valuable data so we could understand and control better the inner workings of our operations.”
C&C will implement Galaxius, a production management system that documents the whole journey of a garment from sampling to delivery.
Batches of garments will be assigned QR codes for each element of its manufacture with an expected timing for completion for each part of the process. As the batch moves down the production line the machinist uses a handheld device to scan the code at the start and finish of the process, recording its progress to completion.
The data is transmitted, processed and then displayed in real-time on a web-based management platform, which gives the leadership team visibility of the production line.
The introduction of real-time and accurate data is expected to have a transformative impact on C&C.
By breaking down a garment’s production into separate elements and applying a timing for each part, the business will know exactly how long it will take to produce a set number of garments and the manufacturing cost.
C&C will be able to plan its production effectively, accurately assess factory capacity and provide customers with realistic delivery dates.
Increased visibility of KPI data and results in real time will allow C&C to gather and track manufacturing data to enable factory performance, and the ability to assess new methods of working to make incremental improvement to productivity.
The simpler production planning system will enable the factory manager to focus on improving processes further.
The improved efficiency will remove the need for overtime, reducing factory running costs by up to 20% during peak periods.
It will give C&C the opportunity to introduce performance related pay and incentivise its staff to improve their productivity in order to receive higher pay and bonuses.
“At the heart of this new system is the introduction of well-informed decision making based on accurate and real time data,” Victoria explained. “By combining better production control and incentivising our workforce we believe we could increase productivity by 40%, while maintaining the highest quality.”
“The profitability of our factory very much relies on the efficiency of the sewing staff and the accurate costing of operations. Galaxius will allow us to make decisions that will directly impact productivity which in turn will immediately increase our bottom line.”
In addition, as every stage of the critical path is tracked, C&C will be able to offer its customers full traceability of their garment through the factory and provide information for ethical and sustainable audits on who made their clothes.
“With traceability being a huge part of the sustainable fashion agenda, the ability to share this data with customers will give us a competitive advantage when pitching for new business,” Victoria said.
C&C hope to improve the user interface to enable individuals to visually see their performance in real-time.
Other future plans include investing in automated machinery, in particular a robo cutter and spreader to increase the speed and amount of cut working flowing to the production lines and other automated machines that will remove time from non-sewing processes thus increasing overall efficiency on the line.