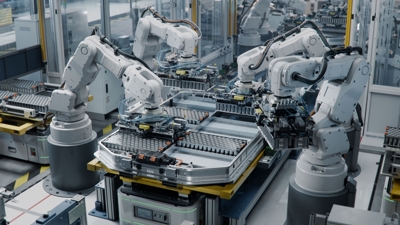
Automation is transforming the manufacturing landscape, offering SMEs and micro manufacturers the chance to boost efficiency, reduce costs and improve product quality.
While automation reduces repetitive and manual tasks, concerns about job security often arise. However, rather than replacing people, automation can empower them, allowing workers to focus on more valuable, creative and strategic roles.
One major challenge is managing this transition effectively. When Label Apeel introduced automation, its customer service team feared job displacement. This concern is common, but with clear communication and upskilling, employees can see automation as an opportunity rather than a threat. At Label Apeel, automation streamlined processes while allowing employees to shift towards more engaging, customer-focused work.
This shift is happening across the manufacturing sector. For example, robotic arms now handle intricate assembly processes with brilliant precision, while automated quality control systems use advanced imaging to detect defects faster than human inspectors. AI-driven predictive maintenance is also preventing costly breakdowns by identifying equipment issues before they cause downtime. These automations improve efficiency and accuracy, but they still rely on human oversight, problem-solving and strategic input.
Instead of replacing jobs, automation should be seen as a tool that complements human skills. Collaborative robots (cobots) are increasingly being used to assist employees on production lines, handling repetitive or physically demanding tasks so that staff can focus on more skilled aspects of assembly and quality assurance. Machines excel at speed, precision and repetitive tasks, while people bring creativity, problem-solving and emotional intelligence. When integrated effectively, automation and human expertise create a more dynamic and innovative workplace.
However, one of the biggest obstacles is managing how automation impacts the workforce, and the essential role people continue to play in this shift. While it’s natural for employees to have concerns about job security, the reality is that they remain indispensable in an automated world.
The workforce of the future isn’t about choosing between humans and technology, it’s about collaboration. Manufacturers that embrace automation while investing in their workforce will stay ahead in a competitive market.
For SMEs and micro manufacturers ready to adapt, Made Smarter provides funding and support to help integrate digital technologies like automation, AI, cybersecurity, and more.
The next programme begins in April 2025, apply today and take the first step toward a smarter, more efficient workforce https://www.madesmarter.uk/start-your-digital-manufacturing-journey/.