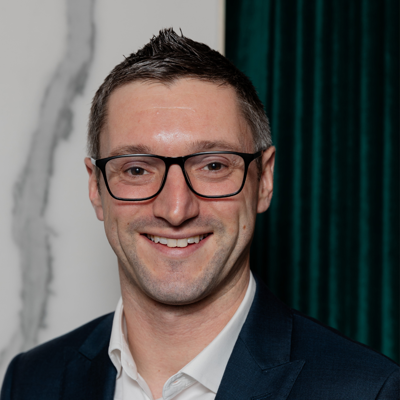
In the January 2025 edition of Food Processing magazine, Editor Suzanne Gill asked industry spokespeople their thoughts on the importance of technology in the Food & Beverage industry.
One of the spokespeople interviews was Made Smarter Technology Adoption Specialist Will Kinghorn.
Read the full articleWhat do you think are the three most important technologies that engineers in the food processing and manufacturing sector should be looking at in 2025 and why?
Data Science
Over the last few years data capture and analytics technology adoption has gone from a ‘nice to have’ to a ‘must have’.
The levels of automation now in most factories means rich and useful data are abundant both live and historical.
The key is understanding what you want to do with it. That means identifying your challenge, whether that is an improvement in production, quality, logistics, energy use, or back-office tasks like sales, and then developing a plan to tackle with the right tools and the right skills.
When it comes to data analytics, there are plenty of useful analytics software options out in the market, and plenty of opportunities to test to see if it is a good fit for your business, through free trials and funded data science advice from support agencies.
By approaching data science in a considered way, a manufacturer can achieve huge gains to optimise decision-making around pricing, promotion, planning, stock control, scheduling, workforce management and energy analysis.
Unfamiliar Automation
With a dwindling labour pool, the costs of labour are rising, leaving food manufacturers to understandably focus on machinery to get the job done.
If critical processes have already been automated, then 2025 should be about solving process challenges using technologies that are common in other industries.
Let’s say you’re a baker who has automated the mixing process. The unfamiliar automation could be a robot to automate packing and palletising at the end of the production line. Other key areas robotics or automation could help are machine loading and unloading, transferring products, and erecting boxes.
In any instance, it is important to take a considered approach to adoption to avoid wasted time, money and effort.
A good approach is to tackle a quick win, something that provides a faster return on investment. This also offers employees a proof of concept that demonstrates that they can benefit. Instead of losing their jobs they become more interesting and skilled.
AI Boom
If 2024 was the year AI became the buzzword, 2025 will see AI with a place at the top table when discussing the digital transformation of food manufacturing.
AI can enhance operational efficiency, optimise production processes, improve supply chain management, and enable better quality control.
Predictive maintenance powered by AI already helps manufacturers anticipate equipment failures before they occur, reducing downtime and increasing overall productivity.
AI could now accelerate product innovation by simulating flavour profiles, textures, and nutritional content, allowing manufacturers to create new food products more efficiently and respond to market trends faster.
A good example of what is happening now comes from a recent collaborative R&D project, supported by Made Smarter Innovation, involving Singular Intelligence, Sainsbury’s and food producer Cranswick. They developed and tested an AI solution to interpret market signals to mitigate the risk of supply-demand imbalances.
The trial cut Sainsbury’s food waste by up to 70% on some products, while increasing availability by up to 5%. Meanwhile, Cranswick reduced its oversupply of pork sent to the retailer by over 15%.
Innovations like this demonstrate how far AI has come in its application to food manufacturing challenges. It is only going to get bigger.