If you’re not sure where to start, seeing what others are doing to reduce their carbon emissions is a great first step to take. You should seek to share knowledge not just with the businesses in your network, but across industries and country borders.(4)
We must get beyond the desire to keep innovations and solutions to ourselves. Community and collaboration is the new currency, and it’s incredibly important to promote intelligence-sharing in order to benefit both the economy and the environment. (5)
So, seek advice from experts and discuss your concerns with others that are in a similar position along the digital journey as you. By doing so, you’ll help achieve net zero-related objectives more easily, as well as boost operational efficiencies and reach more consumers.
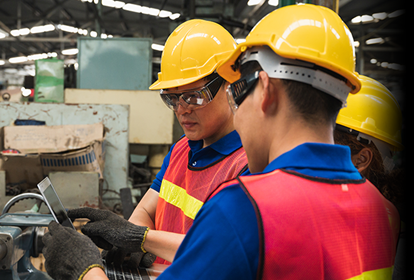
The ultimate guide to making your manufacturing business more sustainable
Your guide to making your manufacturing more sustainable
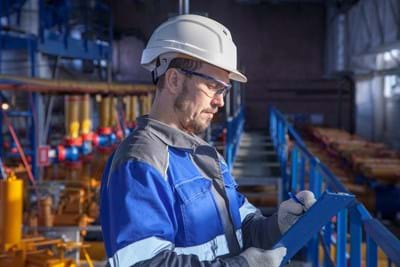
Climate change can no longer be ignored, especially in the UK. Britain is the largest net importer of emissions per capita worldwide. This is because we import products – and therefore emissions – from abroad.(1) As a result, the government is committed to ensuring the UK becomes the first major economy to reach ‘net zero’.
Reaching net zero means taking the necessary steps to reduce emissions in the first instance, and then offsetting those that remain. But the manufacturing industry (together with the transport and storage industries) is the third-largest direct (scope 1) greenhouse gas-emitting sector of the UK economy, at a 15% contribution.2 So, how can we reduce our carbon footprint and become more sustainable? Technology could play an incredibly important part...
The goal is to reach net-zero greenhouse gases by 2050.3 And this isn’t just a target – it’s an Act of Parliament, legally binding the UK to this commitment. Here, we explore how to boost the sustainability of your manufacturing business to help the UK economy meet this goal, as well as discuss how more sustainable practices can benefit your business, its bottom line, and the environment. This guide also highlights how digital tools can play a role in helping you successfully implement these changes, monitor your activity and track improvements in your carbon footprint.
Download the guide-
Connect with others
-
Adopt basic factory efficiency practices
There are many small creators of energy efficiency that manufacturing businesses aren’t utilising – or aren’t yet making the most of.
One very basic example is lighting. Sometimes, it can be as simple as replacing halogen bulbs with the more efficient LED alternatives. Automated lighting systems that adjust according to the room’s occupancy or daylight availability can also be invaluable if employees move between numerous buildings and work areas (and often unnecessarily keep lights on). Day and night switches can additionally be used to manage outdoor lighting effectively, and motion detector sensors can be installed too.In the same way you can only keep lights on when necessary, you can ensure you only run equipment when needed. For this, it’s wise to reduce the operating pressure of your air compressor, as well as check to see if there are any leaks – compressed air alone contributes considerably to overall industrial power usage.
When it comes to your machinery, it’s a good idea to put regular cleaning and maintenance in place to optimise their performance and lifespans.If your air conditioning and heating systems are older than 10 years, we’d also recommend replacing these with newer, more efficient ones. During installation, make sure that your systems are set to the optimum positions during the different seasons. Insulation will play a role in this. By insulating the roof and walls of the workspace, you can dramatically reduce the energy required to preserve room temperature. Likewise, you can also opt for natural ventilation such as opening a window or building door.
Another couple of basic efficiency practices are optimising appliance settings, like your fridge, and checking the lagging on pipes. The latter will allow you to see if they’re insulated or not and then take the right course of action.
-
Employ more advanced efficiency techniques
There are a number of other key ways in which you can act on efficiencies to help reach net zero, and they’re specifically related to employing technologies.
Reducing waste through Digital Twin technology (which creates a digital replica of physical assets)6 and additive manufacturing (3D printing) are two such examples.
Additive manufacturing boosts digital flexibility and efficiency. This is through tools that direct hardware to deposit material, one layer on top of each other, in incredibly precise geometric shapes. The result is lighter and stronger parts and systems.(7) It reduces lead times and generates opportunities that extend a
product’s life cycle, and so lends itself to the circular economy.(8)You can also look at the opportunities to generate your own energy on-site – this can then be stored with battery technology and result in significant CO2 savings.
Predictive analysis, gained through artificial intelligence, allows you to have a better understanding of demand. Additionally, it can pinpoint any inconsistencies and optimise production. For instance, you may use it to automate flexible dosage inputs and quality checks. You also have the option to control production systems in real time, enabling you to reduce the chance of breakdowns and optimise machine idle and start-up times.
Robotics are incredibly valuable too – this technology can automate numerous parts of production to improve your business’ productivity and the use of assets. Then there are industrial digital technologies which effectively sort waste into fractions before processing and treatment. Whichever way you want to make your business more efficient, always conduct ideas testing in a safe environment first. -
Use big data
Many businesses have found that the data provided by the tools is just as valuable as the technologies themselves. Through implementation, they can discover ways to further improve processes and increase efficiencies.
Makers can input as much information as they’d like – and the more data, the better quality the analysis. They can pinpoint exactly where emissions are produced, and the actions they can take to lower or eliminate them. This data can also be benchmarked and shared with others. Through these analytics, you can even retrofit your existing manufacturing processes.
Digital technologies can give enterprises a better understanding of their energy usage, plus make intelligent moves to increase efficiencies. These technologies include AI, IoT and blockchain. The latter can be used for enhanced transparency, as well as making it easier to track carbon emissions.
-
Upskill and educate your workforce
What about those operating the technology? A team with the right skills and knowledge to get the most from
the tools will also be required.There is, however, currently a low-carbon skills gap. It has been found that 10% of the UK workforce – especially in industries like manufacturing, construction and transport – should be reskilled and effectively educated to meet the needs of the future green economy.(9) You’ll likely have to focus on bridging this gap
within your business.
It’s also a great idea to share your energy-saving initiatives with employees. Help them see the impact it will have, the small things they can do, and be open to their ideas and willingness to use technology in order to achieve your goal. -
Decarbonise heat and power
There are a few different pilot schemes that are reducing or removing carbon emissions from the generation of heat and energy. These fall under the categories of alternative energy sources, more efficient uses of energy, and negative-emission methods.
They include:
• Replacing natural gas with hydrogen (which doesn’t produce any greenhouse gas emissions)
• Carrying out the electrolysis of water
• Generating and sourcing renewable energy, such as solar PV and wind
• Electrification (switching from gas, petrol or diesel to electric – this is suitable if the electricity mix on the grid is generated from renewables)
• Combined heat and power (CHP)
• Installing heat pumps to lessen the emissions from heat-demanding processes
The use of green technologies in these methods are carried out by the green technology and services sector, which has hundreds of contributing businesses in the North West alone.(10) -
Consider recycling options
Digital tools can enhance your recycling approach, and simultaneously benefit your business. Advanced technology is available to effectively recycle chemical content – proving particularly helpful for fashion manufacturers.
Mechanical and novel chemical recycling techniques can also be utilised to reduce primary plastic production, as well as cut down on your enterprise’s manufacturing waste. Electric arc furnace technology can be scaled for greater scrap steel reuse, providing a clean substitute for emissive blast furnaces.
Recycling is key to creating a circular economy – but it should be noted that it only makes up a part of it. You’ll need to also think about how waste can be either designed out of products or processes, or re-used to help build a new item.
-
Cut your waste
Waste reduction is another very basic method for boosting your sustainability. After all, if you address waste, you can make carbon savings through the reduction in materials – not to mention boost your profitability.
It’s a good idea to focus on those products or processes that make the most noteworthy impact (damaged or scrapped product by weight or value, for example). Some manufacturing businesses opt to appoint a waste prevention team or take a waste audit to ensure this is actioned effectively.
An efficient inventory management system can also go a long way, as it will ensure you minimise the amount of excess raw materials in stock. You can also reduce volume by separating hazardous from non-hazardous waste. In terms of packaging materials, these can be redesigned to lower the amount of materials used and instead incorporate reusable or recyclable packaging content.
Then there is the ‘recover, reuse, sort’ approach, which does exactly as it says on the tin: you recover as much waste as possible, reuse it, and then effectively sort it so that recyclable items get to the right place. A ‘preventative maintenance schedule’ is another idea, allowing you to be proactive and prevent any machinery breakdowns rather than lose time, money and energy due to unexpected issues.You should also ensure your warehouse is labelled and organised effectively, as well as minimise the water usage in your operations as this contributes significantly to manufacturing waste streams.
-
Reduce transport emissions
If your manufacturing involves transportation, lowering emissions could be as simple as opting for electric vehicles (EVs). Technological advancements have resulted in more cost-effective batteries, and drivers can now use any public charger. Businesses can even access Office of Low Emission Vehicles (OLEV) grants to invest in EV charge points.
There is also the option of hydrogen fuel cells for heavy goods vehicles and buses. This allows for more rapid refuelling, a long range, and the possibility of cutting infrastructure costs.
Additionally, you could consider the use of augmented reality (AR) and virtual reality (VR). These advanced technologies mean that transportation from one location to another may not even be necessary. In many situations, you can gain what you need without having to travel at all. -
Share knowledge
Don’t keep your learnings to yourself. Remember the very first point made in this guide, and impart what you’ve found out through your sustainability initiative and the use of technology with others in the industry too – whether that’s a specific tool, a particularly good practice, or an outcome of data analysis.
Additionally, share knowledge with your customers and those in the supply chain. Not only can divulging your steps to sustainability make your business a more attractive prospect to these groups, but it may ultimately lead to other businesses being able to reach their own netzero goals as a result.
-
The ultimate way to start boosting sustainability?
- Get support - It’s one thing to consider using new technologies, but it’s another thing entirely to actually have the resources to do so. If you’ve hit a stumbling block when it comes to determining (or financing) the best tools for your particular business, turn to Made Smarter.
Our programme has been specifically developed to help manufacturing enterprises just like yours embrace technologies. We spend the time to understand your business’ needs before providing independent, impartial advice on the most suitable tools. We also deliver tailored funding and support. A number of SMEs we’ve helped are already on their way to reaching their goals toward net-zero emissions.
We help in other ways too, from fully funded student placements to our Leadership Programme. If you’d like to boost the efficiencies in your SME by maximising on these new technologies, get in touch. Simply fill out our contact form. You can also discover how we’ve helped many businesses in the industry already by browsing our case studies. One such example is Blends Holding who, with our support, are forecasting improved efficiency and a packaging reduction of 25%.
- Get support - It’s one thing to consider using new technologies, but it’s another thing entirely to actually have the resources to do so. If you’ve hit a stumbling block when it comes to determining (or financing) the best tools for your particular business, turn to Made Smarter.
-
A case study for success: Blends Holdings
Family-owned Blends Holdings were using outdated, paper-based systems, along with a mix of software which didn’t communicate to one another. And so they looked into cloud-based technologies.
Today, they have a food manufacturing-specific ERP software system, which brings together the different parts of their business, and enables live and remote analytics and monitoring.
This will lead them to improve efficiency by 50%. Additionally, as the new software gives them greater access to data, they’re predicting a 25% reduction in packaging. On top of this, they are able to speed up processes and increase the region’s GVA by £1.5m over the next three years. You can read their case study in full here.
-
Sources
- 1 https://www.ons.gov.uk/economy/nationalaccounts/uksectoraccounts/compendium/economicreview/october2019/thedecouplingofeconomicgrowthfromcarbonemissionsukevidence
- 2 Source Accenture analysis available upon request. Please contact Gemma Baker,
Sustainability Director at Accenture Strategy, to find out more. Based on 2018 data from
the Office of National Statistics. - 3 https://researchbriefings.parliament.uk/ResearchBriefing/Summary/CBP-8590
- 4 https://www.theccc.org.uk/wp-content/uploads/2019/05/Net-Zero-The-UKscontribution-
to-stopping-global-warming.pdf - 5 https://www.aldersgategroup.org.uk/asset/1357
- 6 https://fslci.org/wp-content/uploads/2018/Slides/Sessions/Session_5_Prox.pdf
- 7 https://www.ge.com/additive/additive-manufacturing
- 8 https://www.sciencedirect.com/science/article/pii/S0959652619311850
- 9 https://www.aldersgategroup.org.uk/asset/1357
- 10 https://www.green-growth.org.uk/network/search