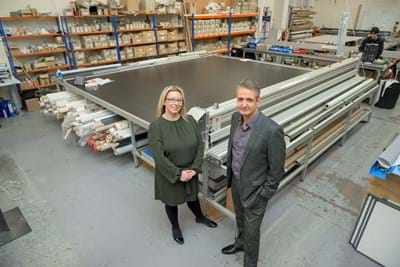
A family-owned window blinds, shutters, curtains and awnings business is continuing its manufacturing operations in the UK rather than looking abroad after receiving support from Made Smarter West Midlands.
Reynolds Blinds was started in 1993 by brothers John and Iain Pickup from a small shop in Erdington, Birmingham. The business has grown steadily over the last three decades and now has four showrooms in north and south Birmingham, Banbury and Oxford.
A total of 30 people are employed throughout the business, with its head office and manufacturing operations taking place at its premises in Melchett Road at the Kings Norton Business Centre.
Its orders are split equally between retail customers and commercial businesses and organisations, with clients including Thames Valley Police, University Hospitals Birmingham NHS Foundation Trust, Aston Martin and NFU Mutual. Reynolds Blinds wanted to update its Vertical Blind Manufacturing Machine for cutting, punching and pre-folding vertical blind fabrics. John heard about Made Smarter West Midlands through the Greater Birmingham and Solihull Growth Hub.
After receiving advice and a grant through the Made Smarter West Midlands programme, a new Automated Vertical Blind Manufacturing Machine will soon be installed, leading to the retention of jobs and the headquarters continuing to be the base for their manufacturing operations.
John, who is a director at Reynolds Blinds, said: “As a result of obtaining the funding from Made Smarter, we have secured three jobs and we are pretty confident about creating more jobs going forward.
“It will allow us to programme the machine directly to our sales order processing equipment to help reduce errors.
“It is a higher capacity machine so we can make more blinds in a shorter time and we’re hoping that the downtime will be substantially reduced – we were previously having a machine down for about six hours a week.”
Case Study - Reynold BlindsHaving the experience of Made Smarter West Midlands and the MTC to call upon when deciding which machine to buy had been extremely valuable.
John Pickup, Director, Reynolds Blinds
Reynolds Blinds has always invested in the latest technology to manufacture its made-to-measure blinds, shutters, curtains, awnings and conservatory fabrics.
But one particular piece of machinery needed repairing because it was constantly breaking down, losing valuable time to meet orders.
John explained: “When we approached the company that had always repaired this machine, we found out they had gone out of business.
“The machine was 20 years old but it wasn’t due to be replaced for another few years so we were stuck because it makes the material strips to specific measurements.
“We had two of these machines. The first is in bits now because we have taken parts off it to keep the other machine running."
John remembered hearing about Made Smarter West Midlands through the Growth Hub and after he approached Lucy Cross, the Digital Transformation Specialist for Greater Birmingham and Solihull, she came to Kings Norton to visit John.
She arranged for the MTC, one of Made Smarter West Midlands’ strategic partners, to join the visit and offer advice on which Automated Vertical Blind Manufacturing Machine would most suit Reynolds Blinds’ requirements.
John said: “When we reached out into the industry for advice, we were told to offshore work, which appears to be the current direction of travel for many of our competitors.
“We were not comfortable with that. We were more interested in championing manufacturing in the UK and Birmingham in particular and preserving jobs.”
Lucy Cross said: “My involvement was in the initial diagnosis of Reynolds Blinds, making introductions to the MTC, and supporting the business through the application process.
“The new machine will help John and Iain to improve their business’s reputation in regards to commercial contracts to help with their growth because they had an ineffective piece of machinery, so now they will be able to deliver their orders on time without any reputational risk.”
Lucy helped John complete the application form for a £20,000 grant from Made Smarter West Midlands, with Reynolds Blinds adding a further £30,000.
John said: “We approached three possible suppliers. The first was a cheaper machine but the technology was quite outdated and wouldn’t have actively improved on what we already had.
“The second option was a very advanced machine but the cost was three times what we have ended up with, so we went with the model in the third option which had up-to-date technology, met our requirements, and the brand is a manufacturer that we have used before and trusted.
“The machine pulls fabrics off a roll and then cuts, creases and seals it so it is ready for the blind.”
Tomas Novais, Senior Advisor, Digital Transformation, at the MTC, said: “The investment made by Reynolds Blinds, with support from Made Smarter, will allow the business to continue to grow and differentiate itself in an extremely competitive market.
“Reynolds Blinds is another great example of how businesses manufacturing locally can compete in a global market by providing quality products and great service, supported by innovation and investment in digital technologies."
John said having the experience of Made Smarter West Midlands and the MTC to call upon when deciding which machine to buy had been extremely valuable.
“We knew the type of machine we wanted but it was good to have a second pair of eyes on the project from the MTC,” he said.
“Having someone with experience in digital technology like Tomas was important because he was able to draw parallels from previous industries.
“We have ordered the machine, following the advice we had on the best way to integrate the machine with our own computer systems to give the maximum benefits that the new equipment brings.”
John is optimistic for the business’s future after keeping its manufacturing base at its Birmingham HQ.
“We had a tender with a two-day turnaround which we managed to complete because we have kept manufacturing here rather than going abroad and that will hopefully lead to providing blinds or curtains for 180 apartments,” he said.
“The current machine can only be run by one or two people, but the new machine will be able to be used by all members of staff and can be left alone while other tasks are carried out. This will improve our efficiency and increase our flexibility in the factory to move staff where we have demand in other areas.”
Reynolds Blinds will also continue to invest in apprentices. John added: “When we first started the business as youngsters, we found employing experienced staff quite difficult and we wanted to find very motivated and skilled members of staff and, as a result, we joined an apprenticeship scheme.
“Evita Greve has completed her studies in Business Management and Chelsea Geary has completed her professional accountancy exams and now heads up our accountancy department.
“Chelsea and I went to Downing Street to meet Education Secretary, Gillian Keegan, along with other companies and their apprentices to highlight the difference these young people have made.”