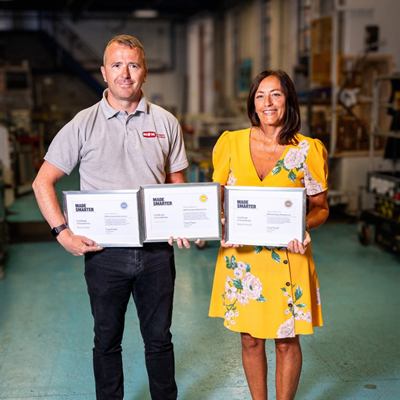
A Manchester aerospace manufacturer has invested in Digital Twin technology to redesign its new factory and unlock production and capacity planning in the future, thanks to Made Smarter funding.
Cutting-edge Digital Twin technology from Siemens, will enable the business to optimise the design and layout of the factory floor prior to build by generating a digital replica of the plant. Made Smarter has supported MSM to broaden the scope of the project to be able to simulate individual production processes to identify, streamline and maximise operational efficiencies. This pairing of the virtual and physical worlds will give MSM never-before-seen analysis of data and monitoring of systems to manage problems before they even occur, prevent downtime, and even plan for the future by using simulations.
The technology will accelerate MSM’s growth. Without Made Smarter funding we wouldn’t have committed to such an advanced level of simulation. Our plan was always focussed on design as a discrete project. This extra investment means we get maximum value from the technology in the future. It also means that we could do it immediately rather than delaying – propelling us forward by years.
Mike Rothwell. Operations Director, MSM aerospace fabricators
The cumulative effect of these improvements is that MSM will become more productive. MSM predicts a growth rate up to 20% a year, allowing it to break the £10M turnover mark in the next three years, which could bring a £401,000 boost to the region’s GVA, with many new jobs expected to be created over the next three years.
Made Smarter also helped MSM plan for the future with a Digital Transformation Roadmap which highlighted other areas of technology to potentially explore. MSM has purchased an Ultimaker 3D printer to assist its R&D and new product introduction programmes. Specialising in metalforming, MSM manufactures complex components in high temperature metals. Additive manufacturing has been adopted for rapid production of prototypes, inspection fixtures and press tooling.
The example shown is part of an aircraft exhaust which was proving difficult to align and inspect to the fine tolerances the customer demands. MSM’s engineers designed and manufactured this fixture in 2 days to allow simple go/no go gauging and enable accurate CMM laser scanning. MSM is committed to further adoption of IR4 technology, the 3D printer is complementary to its existing metalforming simulation capability. The company has invested in other advanced manufacturing technologies including robotic welding and enrolling staff onto Industry 4.0 leadership courses. MSM has an 80+ year heritage in this industry, and is a forward-thinking, digitally compliant SME at the leading edge of advanced technologies with an exciting future ahead.