Eliminating wasteful activity within your business is a branch of lean thinking, which outlines overproduction and over-processing as two key areas of waste management.
It’s important to bear in mind that exceeding customer demand leads to added costs, as anything a client is unwilling to pay for is essentially waste. Similarly, adding unnecessary features to a product increases its price tag, potentially turning it into something that clients are again not willing to pay for. Taking the time to measure productivity for profit ensures you’ll make the most of your resources.
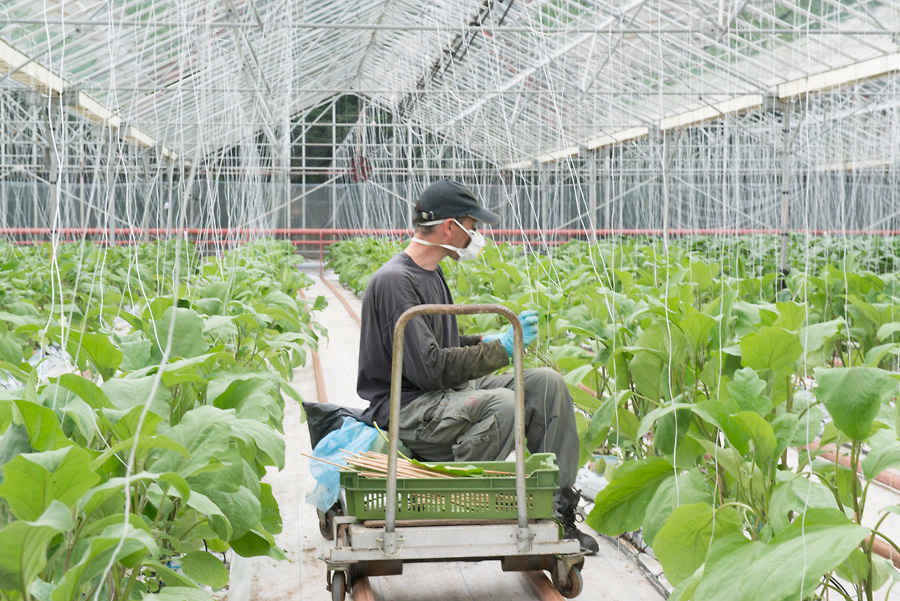
A manufacturer’s guide to work smarter
Do more with what you have
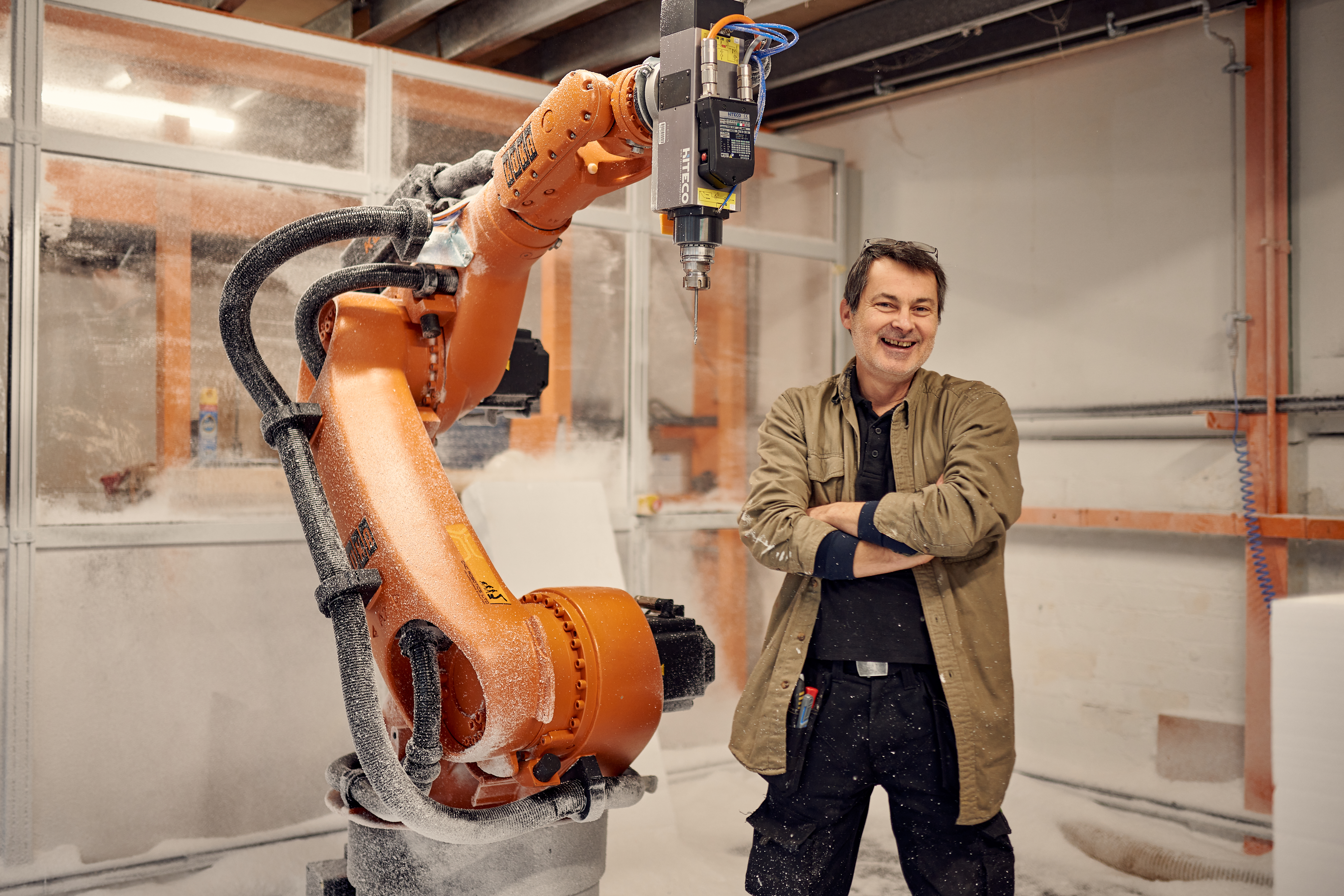
How to get more from your resources, time and people
Today’s challenging economic climate means one thing: capitalising on existing resources is more critical than ever. By taking steps to improve efficiency and maximise productivity, UK manufacturers can reduce wasted product, wasted ingredients, and wasted time – in turn helping to combat rising costs
Made Smarter Work Guide-
Lean thinking
-
Recover, recycle, and resell
A lot of the time, waste materials in manufacturing can be reused directly within the business.
That’s why it’s important to recover as much waste as you can – this can be done using various techniques including electrolysis, filtration, reverse osmosis, and centrifugation.
Recycling materials by turning them into a new substance or product also helps to minimise
waste. Or, if you no longer have a use for a particular item, consider selling it to another manufacturer who will. -
Time
Earlier, we discussed unplanned downtime as one of the biggest losses for manufacturers.
However, the issue isn’t always due to unexpected events – planned stops can also interfere with production times.
Examples of planned stops include safety checks before a machine is able to run, tooling adjustments or repair, cleaning, or even employee breaks. Even though this downtime is
categorised as ‘planned’, it still counts towards production losses as it’s something that can be improved upon.
With the help of IDT experts, you can use digital tools to improve the efficiency of your factory floor and reduce the duration of planned stops. This will, in turn, boost your reaction and order fulfilment time – allowing you to meet the needs of your customers quickly, and retain and
attract new customers in the long term. -
Digital Twin technology
Another way SME manufacturers can maximise productivity and support growth is by putting data at the heart of their digitalisation journey – a step taken by almost 75% of SME manufacturers supported by Made Smarter. An example of this in action is a plastic card manufacturer who implemented a bespoke solution that can read a card, check it against a data file in real time, and then encode it. Software then interrogates the manufacturer’s customer database for the personalised data for the card, and then organises print jobs for the day. The result is an 8% increase in turnover.
Play equipment manufacturer Playdale has drawn on analysis from its real-time performance and predictive maintenance data to understand the savings from improved efficiencies as well as reduced downtime, tooling spend and maintenance costs. They’re then going to replicate this across their other legacy equipment -
People
Of course, your business is primarily made up of people. It stands to reason, then, that one of the best ways to reduce waste throughout your organisation is to encourage a waste management culture. This could involve something as simple as setting targets, and making these visible throughout the day – this not only offers direction, but it also motivates employees to participate in the process.
Another small but effective method is reminding staff to turn off machinery and lights when it’s safe to do so. Initially, you might want to create signs to place near switches, but eventually, it will become second nature.