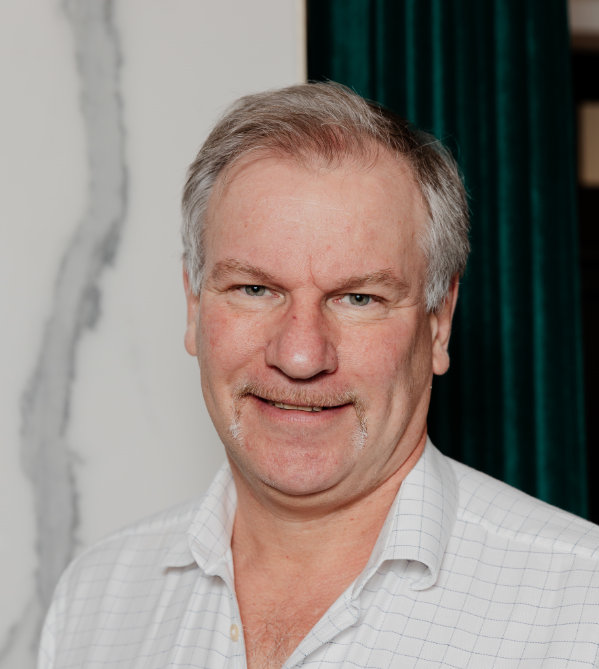
The origins of the Made Smarter adoption programme are wrapped up in UK manufacturing’s long standing productivity puzzle.
In 2016 manufacturing contributed £177bn to the UK economy, accounting for over 50% of UK exports 204 and over 70% of R&D. But like all sectors of the economy, it was struggling to recover from the financial crisis.
UK labour productivity at the time was 20% below the USA, France, and Germany. Economists and industrialists who previously accepted the cyclical nature of a boom and bust UK economy were left scratching their heads at the growth flatline which was seeing the UK fall behind global competition.
Industry's failure to embrace advanced technologies and its continued reliance on human workers to do repetitive unskilled tasks was blamed for the lag.
The winds of change
In 2017 the UK Government published its Industrial Strategy with the aim of solving the productivity puzzle, backing businesses to create good jobs and increase the earning power of people throughout the UK through investing in skills, industries and infrastructure.
A key pillar to the strategy was the ambitious industry-led Made Smarter Review into industrial digitalisation.
The Made Smarter Review
Led by Professor Juergen Maier, the then CEO of Siemens UK, the report demonstrated how the application of digital technologies - such as artificial intelligence and robotics, data analytics and additive manufacturing - had made transformational improvements to productivity to early adopter businesses who had already exploited their potential.
It then set out the significant opportunities to be gained by the faster development and adoption of these technologies across all UK manufacturing sectors over a decade, including:
● Increasing productivity by at least 25%, output by £455bn and manufacturing sector growth by up to 3% per year
● Raising exports through international competitiveness
● Strengthening UK supply chains and creating new value streams
● Addressing regional economic disparities;
● Creating 175,000 jobs
● Upskilling 1M industrial workers
● Reducing CO2 emissions by 4.5%
In a rallying call to recapture the UK’s industrial spirit as a nation of ‘creators and makers’, the Review laid out a bold and ambitious plan to equip the UK with the means to fully embrace the next industrial revolution with four priorities: innovation, adoption, leadership and skills.
The proposal called for a National Adoption Pilot programme focused on offering SME manufacturers access to a support package, which could boost growth, productivity, efficiency, decarbonise and create high value, well paid jobs of the future.
Why the North West?
In 2017 there were around 14,500 manufacturing SMEs in the North West, 5.5% of all SMEs compared to 5.1% nationally, supporting 318,000 jobs or 9% of the region’s total workforce.
Manufacturing accounted for 16% of the region’s total output – the third highest of any UK region - and 10% of the UK’s manufactured exports, half of which went to Europe.
But it also suffered from productivity levels which were 10% below the UK average, and a higher proportion of workers in low paid employment than the national average.
Testing an adoption programme in the North West also aligned with pan-Northern and regional priorities.
The report also highlighted ‘digital’ and ‘advanced manufacturing’ as two of four prime capabilities alongside ‘energy’ and ‘health innovation’ to drive growth across the region.
It forecast that by 2050, realisation of these capabilities could increase the region’s GVA by 15% higher, productivity by 4% and create 850,000 additional jobs.
Navigating the challenge: a new approach
The pilot was an opportunity to design a new kind of business support service for manufacturers that tackled the key barriers preventing them from adopting technology: time, knowledge, and capital.
Naturally, offering funded access to expertise around digital strategy, technology and skills were a big draw for manufacturers. But crucially it established the core principle that people are at the centre of adoption, and technologies are valuable tools.
Trust and agility
This is where pairing technology and Organisational Workforce Development (OD) specialists with a business, to give them access to expert and impartial advice, came into its own.
The approach developed trusting relationships with companies looking for advice, recommendations, and a critique of their investment and digital adoption plans. The programme also responded quickly to the feedback from manufacturers.
The process of assessing a manufacturer’s product, processes and people changed to gather more views from across the factory, rather than just one individual's perspective. A two-day digital transformation workshop allowed technology and skills experts to develop a road map to address business challenges and priorities.
Additional feedback from businesses for a more time-efficient process and to broaden the input from across an organisation, and prompted a further redesign of the service. The two-day workshop was streamlined to a few hours, enabling an effective, tailored ‘package’ of services in a fraction of the time.
A robust model
Listening, learning, and adapting to the needs of manufacturers has ensured the programme remains relevant and practical. It has established a robust delivery model that has helped businesses weather the challenges presented over the last few years.
To find out more about the programme please download our Impact Whitepaper